A Comparative Study for Modelling Filler Material in Metal Additive Manufacturing Processes
Additive manufacturing processes are increasingly used for designing metallic parts with complex geometries. The current needs are focused on the manufacturing of large-scale parts, typically of meter range. However, for such dimensions, the traditional trial-and-error methodology used to identify satisfying operating parameters becomes very expansive. Modeling and simulation can help both from a fundamental understanding of the physical phenomena and enable design and optimization to reduce the qualification cycle of additive manufactured parts. To be able to simulate large structures with reasonable computational time, particular attention is required in the choice of modeling. The present study analyzes different methods to model the filler material and the layer-by-layer building of a 3D geometry. The traditional material activation technique is compared with Arbitrary-Lagrangian Eulerian methods used to move free surface in vertical or horizontal direction. The heat transfer equation is solved to calculate the temperature field in the substrate and the layers. A thin wall of Ti-6Al-4V titanium alloy is considered. The numerical results are compared with published experimental data obtained during laser metal deposition process. The calculated temperature cycles are compared to thermocouple measurements in the substrate. The calculated melt pool dimensions are compared to those obtained from high speed camera. The computation time obtained for the different numerical methods is discussed.
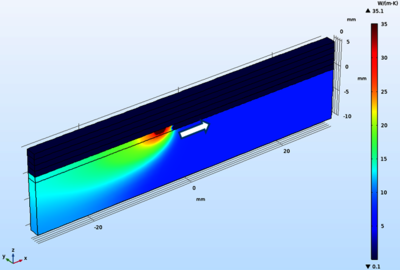