Computational Study on Transition of Oil-Water Flow Morphology due to Sudden Contraction in Microfluidic Channel
The flow morphology of two immiscible fluids in a microfluidic device finds numerous applications such as emulsification, synthesis of nanomaterials [1], lab-on-a-chip devices and biological analysis [2]. It offers many advantages over the conventional macroscopic devices because of its availability for higher surface to volume ratio, ability to handle small volume of fluids, easier process control and reduction in operating cost [3]. But the flows in such microscale devices are mostly influenced by surface and viscous forces, where gravitational and inertial forces have very less impact. Thus, large size flow structures such as slug and plug flow are often encountered, which may not be desirable for processes where higher degree of mixing is required. In this regard, it is very important to identify the flow conditions for developing smaller size flow structures with higher surface to volume ratio. Previous studies have accomplished these objectives by varying the velocity of fluids [4], and fluid properties such as interfacial tension and viscosity [5]. In the present study, we show a simple strategy by which smaller size flow structures could be obtained. Here, we show that by introducing an orifice near the microchannel T-junction, the larger slugs could be transformed into smaller droplets.
The geometry of the computational domain is shown in Figure 1. The “physics-controlled” meshing scheme was chosen with “fine” element size, which created 6876 triangular cells inside the control volume. Silicone oil and water were chosen as the test fluids. The densities of oil and water phase were kept at 1000 kg/m3. The viscosities of oil and water phase were kept at 0.01 and 0.001 Pa s, respectively. The wetted wall condition was chosen with contact angle of 140˚. The oil-water flows were modeled in COMSOL Multiphysics® software. The interface tracking of the two-phase laminar flow was accomplished by the built-in phase field model. The continuity, Navier-Stokes and phase field equations for the incompressible flow were numerically solved by incorporating appropriate boundary conditions. The velocity of oil (Uo) and water (Uw) were fixed at 0.1 and 0.01 m/s, respectively.
Figures 2(a)-2(d) show that a larger size flow structure could be transformed into smaller ones when an orifice is introduced near the microchannel T-junction. The figure suggests that the size of the flow structures decreases with the diameter of the orifice, do. Figure 2 (e) shows how the size of the flow structures, (dd) varies with do. The results from the numerical simulations could be utilized in designing microdevices where smaller flow structures could provide higher mixing of phases.
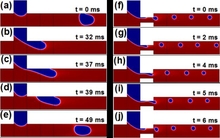
下载
- chaudhuri_presentation.pdf - 1.7MB
- chaudhuri_paper.pdf - 0.87MB
- chaudhuri_abstract.pdf - 0.13MB