Employing COMSOL Multiphysics for the development of a Lightweight Flight Recorder
Serma Ingénierie is a subsidiary of Serma Group, specializing in electronic, electrical, and mechanical engineering. Their primary focus is on guiding clients in developing high-quality technological products and ensuring compliance with standards and regulations.
This work presents the development of a Lightweight Flight Recorder (LFR). A recent legislative change has highlighted the need for this type of equipment. The main challenge involved miniaturizing the technology to make it compatible with light helicopters and ensuring it meets the ED-155 standard. According to this standard, the equipment must successfully pass shock, crush, and fire tests. This presentation aims to describe the work conducted regarding the fire tests, which require the equipment to withstand a flame of 1100°C and 158 kW/m² for 15 minutes.
To achieve this design, extensive work was done in various domains, such as researching high-performance materials, optimizing configuration and geometry, and conducting materials and flame thermal modeling. The latter was one of the most significant challenges to propose a design capable of passing the ED-155 fire test. This was made possible through a combination of experimental measurements and Finite-Element Method simulations using COMSOL Multiphysics. The development of the equipment was divided into three main phases.
Phase 1: Preliminary study on simplified geometry models. The objective of this phase was to identify materials and geometry configurations with the highest thermal performance. This was achieved through intensive use of the Heat Transfer module coupled with parametric studies. To analyze a large number of configurations, the geometries studied were mainly 2D axisymmetric and simplified 3D models.
Phase 2: Fitting of experimental curves to define precise materials models. The goal of this phase was to conduct experimental tests according to ED-155 specifications and use the collected data to define precise experimental and materials thermal models. First, it was necessary to create a heat flux model representing the aggressing flame. Then, experimental curves were fitted by varying materials' thermal properties. The Heat Transfer module combined with the Optimization module was used to achieve the goal of this phase.
Phase 3: Shape optimization. With flame and materials thermal models established, it was possible to design a compact housing for the LFR equipment. The Optimization module was intensively applied to refine the design.
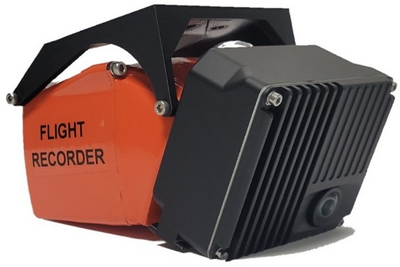
下载
- ortiz_9381_poster.pdf - 0.5MB