Nonlinear Mechanical Modeling of Thermoplastics
The use of thermoplastic materials is increasing and it is becoming more important during the design process to accurately represent the non-linear material response in relevant loading conditions. The COMSOL Multiphysics® software supports advanced modeling capabilities for large deformation analyses, including contact and multiphysics couplings. It is now also possible to use advanced non-linear viscoplastic material models through the External Material Model Interface. In this work we have analyzed the mechanical response of polyether ether ketone (PEEK), a high performance thermoplastic material that is commonly used in orthopedic applications (spinal implants, screws), and in the energy sector (high pressure - high temperature (HPHT) seals). The mechanical response of the material during monotonic loading consists of an initial linear elastic response, followed by onset and evolution of distributed viscoplastic flow. Once the stress becomes sufficiently large the whole material section undergoes energy activated viscoplastic flow. Finally, at large strains the stress-strain response stiffens due to an increase in the entropic resistance. These experimental characteristics are shown in Figure 1.
To model the mechanical response of this material we have used the Three Network (TN) model [1] from the PolyUMod library [2]. This model contains three parallel networks aimed at capturing the response of the amorphous and semi-crystalline domains using a micromechanism inspired framework. In the model the deformation gradient is decomposed into elastic and viscoplastic parts, and the flow behavior is represented using a power-law flow equation. This material model can be directly used in COMSOL software using the External Material Model interface.
The material model was calibrated to the experimental data in Figure 1 using the MCalibration software [2]. The model calibration used uniaxial tension and compression data obtained at strain rates between 0.001/s and 1000/s. Figure 1 shows a direct comparison between the experimental data and the model predictions. The model captures all experimental data with an average error that is less than 15%.
The calibrated material model was then validated by comparing experimental data to COMSOL simulations of two addition experimental tests: (1) a biaxial punch test, (2) a spherical indentation test. These tests were selected because they probe the material response in two very different multiaxial loading modes [1]. The results from the validation simulations are shown in Figures 3 and 4. These figures demonstrate that COMSOL software with the calibrated TN model can predict the non-linear viscoplastic response of this material with excellent accuracy.
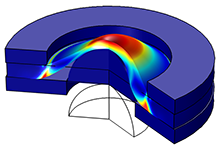
下载
- bergstrom_presentation.pdf - 3.15MB
- bergstrom_abstract.pdf - 0.62MB