Numerical Analysis of the Optimal Design Parameters of a Thermoelectric Microfluidic Sensor
The design of highly-sensitive thermoelectric microfluidic sensors for the characterization of biochemical processes is an important area of engineering research. This study reports three-dimensional numerical analysis of the critical design parameters of a continuous-flow biosensor with an integrated thermopile that significantly increase the detection sensitivity of the platform. The paper discusses the impact of volumetric flow rate, channel height, material thermal properties, and heat sink on the magnitude of the thermoelectric signal. In the platform understudy, the heat generated by the enzymatic reaction between glucose oxidase-conjugated antibody and glucose is converted to an electric output by an antimony-bismuth thin-film thermopile with a theoretical Seebeck coefficient of 7.14μV mK-1. Since this experimental configuration has been implemented in a variety of biochemical analysis [1], particular emphasis in this work is maximizing the detection sensitivity of the device. Computational thermal modeling was performed to investigate the impact of channel height (50 µm, 100 µm, 150 µm, and 200 µm), the volumetric flow rate of the substrate (25µL min-1 and 50µL min-1), using a heat sink, and the microdevice material (glass, PMMA, and PDMS) on the output of the thermoelectric sensor. Experimental data validated the model and provided an excellent correlation between the predicted and measured voltage output. The Conjugate Heat Transfer interface was used to identify the optimal parameter combination that provides maximum sensitivity. The factors that heavily determine the performance characteristics of the thermal microfluidic device include channel height, physical properties of the device materials, inlets flow rates ratio, and the presence of a heat sink in contact with the reference junctions of the thermopile. COMSOL Multiphysics® was used to solve continuity, Navier-Stokes, and energy equations for both fluid and solid subdomains simultaneously. The enzymatic reaction between glucose oxidase conjugated detection antibodies and glucose occurred within the reaction zone and generated heat. Therefore, the heat source for the study was a function of the glucose oxidase and glucose concentrations, the reaction rate constant, and the rate of heat generation. The time-dependent simulations of the temperature distribution and glucose profile were performed for 240 seconds. A step function was used to increase the glucose concentration at t=0 to 55mM followed by a step down to cg=0 concentration after 13µL was introduced into the inlet 1 fluid stream. The inner surface of the microchannel was modeled with non-slip boundary conditions according to the continuum assumption applicable for microscale fluid flow. The Laminar Flow interface was conjugated with the Transport of Diluted Species interface and Heat Transfer Module in COMSOL®. The Transport of Diluted Species interface was used to simulate the flow of glucose within the microchannel. The Heat Transfer Module was used to calculate the temperature difference between the measuring junctions and the reference junctions of the thermopile. Results show that fabricating the calorimeter out of materials with lower thermal diffusivity, reducing the channel height, and eliminating the heat sink at the reference junction of the thermopile increases the sensitivity of the platform by 783%. [2]
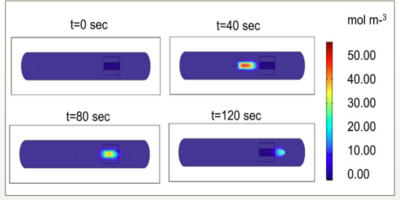