Numerical Study of Heat Transfer Effect of Wire EDM on P91, SS304, Al 1050 using COMSOL Multiphysics®
Wire Electric Discharge Machining (WEDM) is widely used technique for machining intricate geometries. It is a spark erosion, non contact machining process and this gives it an advantage in machining metals irrespective of their hardness [1]. Main process parameters of WEDM are peak current (IP), Voltage (V), Spark on time (Ton), Spark off time (Toff). The ability to machine components requiring high precision makes WEDM process in high demand in industrial applications.
In the present work a numerical model was developed to simulate the heat transfer taking place in the workpiece during machining process. The model was implemented in COMSOL Multiphysics® for general industrial materials used in power plants and other industries. The temperature profile of the workpiece during the spark on time and cooling rate for P91, SS304, Al, was estimated. The temperature profile of the machined surface gives an estimate of the maximum crater size formed during machining. The size of crater accounts for the surface finish of the machined surface which in turn affects the performance of the machined component during service life. A 2D axisymmetric model of workpiece was modelled using Heat transfer in Solids interface of COMSOL Multiphysics®. A general schematic of the model is shown in figure 1. Gaussian heat flux [2], Spark one time, Temperature dependent material properties was modeled using analytic function, step function and interpolation function in Heat transfer module of COMSOL Multiphysics [3]. Convection boundary condition was applied to model the cooling of the workpiece due to demineralised water used as dielectric. Line plot and surface contours in figure 2 and figure 3 shows the size of crater formed in each material and variation of temperature from the cutting edge towards the bulk material respectively. The size of the craters was validated using the scanned electron micrographs of the machined surface cut in same energy.
It is concluded that size of crater formed in WEDM process depends on the electrode material and hence thermal conductivity and heat capacity of the material has significant effect on the surface characteristics of the WEDM machined surface.
Figure 1 Schematic of Numerical model
Figure 2 Temperature profile with crater for P91, SS304, AL1050
Figure 3 Vairation of temperature along the work piece in P91, SS304, AL1050
References:
[1] Dheeraj, K. V. S., et al. "Numerical Simulation of Optimization of Process Parameters of Micro Wire EDM of Al-SiC Alloys Using COMSOL."
[2] DiBitonto, Daryl D., et al. "Theoretical models of the electrical discharge machining process. I. A simple cathode erosion model." Journal of applied physics 66.9 (1989): 4095-4103.
[3] Foong, Chee Woh, et al. "Numerical Study of a High Temperature Latent Heat Storage (200-300 0 C) Using Eutectic Nitrate Salt of Sodium Nitrate and Potassium Nitrate." Proceedings of the COMSOL Conference. 2010.
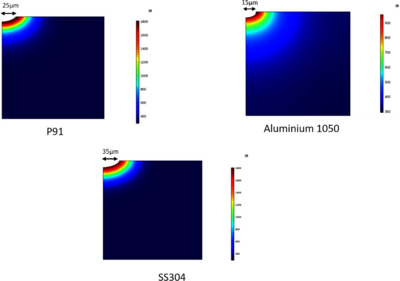