Prediction of Temperature Distribution in a Laser Powered Homogenous Pyrolysis Reactor
Laser Powered Homogenous Pyrolysis (LPHP), a non-isothermal wall-less plug flow reactor using cw-IR CO2 laser heating by fast vibrational–translational (V–T) energy transfer, is a common technique for high temperature pyrolysis in the gas phase with minimal catalytic effect of hot surfaces. Since the heating of reaction mixture is directly applied via the laser heating, heterogeneous catalytic effects on the homogeneous mixture can be disregarded. In LPHP reactor, the vibrational energy of IR laser is absorbed by the introduction of a photosensitizer gas such as SF6 to the reacting mixture where it rapidly converts into heat (translational energy) via efficient relaxation processes. The generated heat is then transferred via conduction or collisions between photosensitizer and reagent gases and further convected or distributed in the reactor environment. Due to the small diameter of laser ray in comparison to the LPHP reactor, the hot zone is confined in the center of the reactor, while the walls stay at approximate room temperature. A detailed temperature distribution in the LPHP reactor is then difficult to ascertain due to the complexity imposed by extremely high temperature gradients in the radial direction. Therefore, the application of COMSOL Multiphysics® to simulate the reactor environment under various experimental conditions such as reactor configuration and dimension, laser power, photosensitizer gas concentration, and carrier gas flow direction can be implemented in order to avoid the unnecessary technical difficulties and experimental errors in direct temperature measurements using thermocouples or other physical tools. A detailed thermal analysis of the gas media with consideration of all Heat Transfer Module (conduction, convection and radiation) on the temperature distribution was performed under a flow condition in continuation of our previous effort for non-flow condition. In order to validate the predicted results, direct thermocouple measurements and chemical thermometer were used.
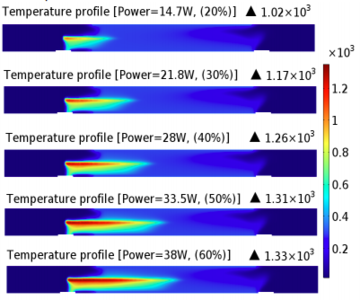