Thermal Modelling of Large Thin Film PZT MEMS Micro Actuators
Large arrays, typically consisting of thousands of devices, made from thin film PZT MEMS technology are increasingly being used in several applications including industrial inkjet printers, adaptive optics and so on. Thin film PZT is attractive because of lower operating voltages and smaller form factors. Despite the smaller operating voltage, thin film devices are operated at much higher electric fields and at higher frequencies. Hence, there is significant self-heating that occurs in thin film arrays. In these arrays, heat is generated in very small volumes of the individual micro actuators, but heat dissipation takes place at the scale of the overall dimensions of the die. This presents a challenging problem in thermal modelling of such arrays since both the small size of the micro actuator and the large dimensions of the overall die must be accurately represented in the model. In this paper, we report the results of thermal modelling of an industrial inkjet printhead die (32 mm x13mm x0.5 mm) consisting of 1420 Thin Film PZT-based micro actuators (55 µm x 1 mm x 5 µm).
The micro-actuators in this die are arranged in four rows each consisting of 355 devices. Two temperature sensing elements are in-built at the ends of each row to enable temperature measurements. Electrical connections are made to every sixth device and the whole row is divided into three groups. Each group can be fired alone or in combination with other groups. In this work, measurements are performed only on a single row. However, the whole die must be included in the model for accurately modelling the heat dissipation, as mentioned above. Each individual device consists of several proprietary thin film layers with thicknesses ranging from a few nanometers to a few microns. We start building the model with a single device with accurate dimensions and then use the array forming techniques in COMSOL geometry tools to build the entire row with a high fidelity. This not only simplifies the construction of the overall geometry with full details of the micro-actuators, but also makes the meshing easier. COMSOL Multiphysics ver. 6.2 with add-on MEMS Module are used in this work. To keep the overall mesh size within manageable limits, only the actuated row is represented with full details of the individual actuators while treating the other rows simply as silicon. This simplification is believed to introduce only small errors since the measured rise in temperatures at the ends of the die are found to be in very good agreement with the modelling results. On the other hand, the model can predict the rise in temperature at the individual actuators which is at least ten degrees higher than the average temperature of the die, as shown in Fig. 3.
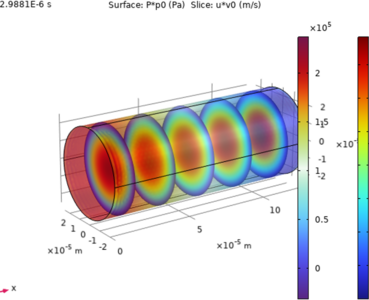
下载
- thermalmodelingpaper.pdf - 0.84MB
- poster_thermal_modelling.pptx - 0.39MB