A 2D Computational Model of a ThermoMagnetic Device
Reducing greenhouse gas emissions and finding new ecological and renewable energy sources are among the biggest challenges humanity is facing nowadays [1] [2]. At the same time, power requirements are increasing constantly, where primary energy consumption is intrinsically accompanied by thermal losses when converted into usable energy, e.g. electricity [3]. These energy losses are usually in the form of waste heat, which is often released into the atmosphere contributing to global warming [4]. Almost 72% of the energy produced by primary energy sources is lost during conversion and more than 45% of the losses are waste heat emitted at temperatures below 100 °C [5]. As an environmental-friendly alternative, Thermo-Magnetic Generation (TMG) is being studied to convert low-grade waste heat into useful and clean energy. This approach is based on the use of magnetocaloric materials and the changes in their magnetization when they undergo a phase transformation as a result of heat exchange with the environment. In this work, a two-dimensional time-dependent model of a ThermoMagnetic Energy Converter (TMEC) device is developed as a first approach to study its magnetic and kinetic response. The physical model consists of a rotor, a permanent magnet assembly, a heat source, and a heat sink. The rotor is made of a magnetocaloric material, and it spins in proximity to the magnetic field created by the magnets. The heat source is a hot water tank with the rotor partially in contact with the fluid, while the heat sink is the environment modeled as air. The magnetostatic fields produced by the magnets are described by Gauss’ law for magnetic fields formulated in the COMSOL Multiphysics® AC/DC module under the Magnetic Fields, No Currents interface. Meanwhile, the thermal energy conservation equation in the Heat Transfer in Solids and Fluids Physic accounts for the heat transfer and the enthalpy flow in the heat source, the heat transfer in the rotor, and the solid-air interface heat exchange. Then, the mass magnetization of the magnetocaloric material is introduced to the model by defining an interpolated function based on experimental data, allowing the kelvin force yielded by the rotor to be calculated and later converted into angular acceleration by the means of a General Form PDE (Partial Differential Equations) interface, where the motion of the rotor is added using the Moving Mesh module with a Rotating Domain node. A time-dependent study is carried out for about two minutes, where computational results for the behavior of the rotor angular velocity, the temperature gradient between components, and the magnetic response of the material are then obtained for a NiMnSn-based Heusler compound, yielding a promising outcome where the force and rotational motion produced by the system can subsequently be converted into mechanical or electrical energy. This model encourages future studies where other parameters of the TMEC can be varied to optimize or enhance the performance of the thermo-magnetic device.
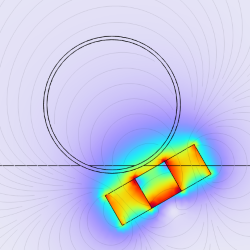