CFD simulation of sublimation flux into a freeze-dryer
Freeze-drying is a widespread technology particularly suitable for heat-sensitive materials such as pharmaceuticals that could be damaged by the high temperature required by traditional drying treatments. A freeze-dryer is composed of two chambers: drying chamber and condenser, connected by a duct. The two chambers can be isolated by closing a valve located within the duct.
This process, which involves the water removal by sublimation, is performed through successive steps: freezing, where the product is frozen at low temperature; primary drying, done at low temperature and under vacuum conditions, during this step free water is removed forming a porous structure; secondary drying, carried out at moderate temperature and under vacuum conditions, to assure the removal of residual moisture strongly bounded to the dried cake.
One of the crucial phases of lyophilization is the primary drying. This step, is strongly influenced by the conditions, in terms of pressure and temperature. During the primary drying, the sublimation flux, produced by ice sublimation, flows through the drying chamber to the condenser, where it is removed by freezing process on the walls, in order to maintain vacuum conditions. Loss of control of chamber pressure is one of the causes of failure of this technique. This can be due to the occurrence of what is called “choked flow”. This condition is reached inside the duct, where the flow section is restricted. In fact, the presence of this restriction results in an increase of the flow speed, which can reach the speed of sound.
For these reasons, the speed that the flow generated by the sublimation process reaches during is pathway is one of the crucial aspect for the success of the process. The aim of this work is to study the fluid dynamic inside the freeze-dryer during the primary drying phase in order to optimize the process and prevent undesired phenomena, such as the choked flow, and investigate the freeze dryer limits due to its geometry, throughout CFD simulations. In particular, the impact of the sublimation flow and process conditions in terms of chamber pressure and shelf temperature on the speed achieved inside the duct has been studied. Moreover, the evolution of the process during time has been investigated trough time dependent solver.
Since from the fluid dynamic point of view, the most critical zone is within the duct, the condensation chamber is not present in the represented geometry. Therefore, the implemented model provides a three-dimensional geometry representative of the freeze-drying chamber, with three shelves on which the product to be dried is stored, and the duct. The product has been represented as a mass flow exiting from the upper side of the shelf. The developed model combines the turbulent model k-ɛ with Heat Transfer in fluids.
Among the first results obtained, it could be seen that chamber pressure is one of the most influential factors on the velocity achieved inside the duct, while temperature variations are less significant. It is expected that the model will allow the identification of limit conditions for the process success.
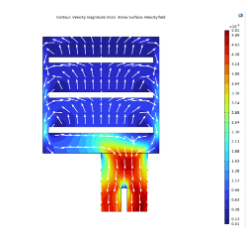
下载
- vigilante_9101_poster.pdf - 1.01MB