Challenges of DC insulating systems for airborne applications
The era of electrical transportation is here and this includes the aviation sector. However, the electrification of airplanes is setting new challenges due to the system operating conditions and ambient conditions during flight which are highly variable. DC electrical systems are constantly gaining ground because they can transfer more power than AC, for the same cable weight. An increased power demand comes with the need for higher voltage which is predicted to reach 3 kV in the near future. The behavior of solid DC insulation systems is closely related to the operating voltage and the ambient conditions. Furthermore, the fluctuations of air pressure and temperature in aircraft applications are an additional risk by decreasing the insulating capability of air. Hence, the proper design of the insulating system is critical, in order to minimize the possibility of electrical discharges on the power train in compliance with the strict weight and size requirements. The electrical conductivity of solid insulators changes with temperature and the electric field strength. This means that the electric field distribution within the insulator will be subjected to changes during flight and ground time of the airplane due to the space charge accumulation. The insulation system may consist of a solid and a gas insulator like air. In that case, the electric field strength reaches its highest value in the insulator with the smallest electrical conductivity. The electrical conductivity of air depends on a number of parameters like temperature, aerosols and irradiation. Consequently, the electric field distribution will change during the flight and it may reach a high value in the air which could lead to an electrical discharge. The accumulated space charge in the body of the insulation adds risk during the “switching-on” of the power train or any other voltage transients. The electric field due to the space charge and that due to the voltage of the conductor are superimposed. Although the phenomenon lasts for a short time, it leads to a considerable increase of the electric field in the insulator. For this work, a comparative study between different insulating materials and for different operating conditions was done using COMSOL Multiphysics® AC/DC Module and Heat Transfer Module. A DC cable was simulated with nominal voltage 1kV, conductor temperature 80°C, air temperatures 50°C and 70°C and electrical conductivity of the air 3 S/m and 8 S/m. It was shown that the choice of a better insulating material can considerably improve the electric field strength distribution and thus reduce the risk for electrical discharges, without adding insulation thickness. Furthermore, it was found that the thermal design of the whole power train plays a critical role for the behavior of the electric field distribution within and around an insulator. It should be emphasized that none of the simulated conditions represents the most extreme case. This proves that a better understanding of DC systems and more sophisticated design solutions are needed in order to reach the predicted level of 3kV with minimum weight and maximum safety.
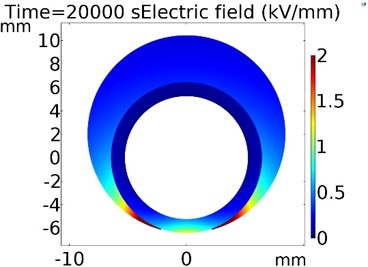