Comparison of FEM simulation with analytic and prototype data of an Axial Flux Synchronous Machine
This Paper presents the results of a FEM simulation with Comsol Multiphysics for an Axial Flux Permanent Magnet Machine (AFPM) and compares them with analytic calculation methods (Matlab, Siemens Star-CCM Suite) as well as test bench measurements of a manufactured protype. The machine is a single gap 15 slot 16 pole design with soft magnetic powder composite as the stator core material. Parameters chosen were magnetic flux density at different points, machine torque, EMF as well as phase inductivities. Difficulties in the simulation arose, because of the complex 3D flux pathing throughout the machine and therefore standard modules of Comsol Multiphysics for electric machine simulation could not be used. Instead, the entire simulation was set up manually. After designing the geometry and combining rotor and stator to two separate unions connected via an Identity Pair for flux conversation, the Rotating Machinery module is used for the physics simulation. Here attention needs to be paid to the magnetic scalar and vector potential definitions for different model domains to ensure simulation success. The standard setting of the rotary machinery interface uses magnetic vector potential in all regions, which would unnecessarily increase the number of degrees of freedom. To avoid this, a mixed formulation was used. All electro-magnetic-active parts (stator core, rotor yoke and windings) of the machine were modelled using the magnetic vector potential formulation. Furthermore, magnetic vector potential formulation was also used to simulate the inner air to avoid simulation instability, but this step increases the degrees of freedom and therefore simulation time. The surrounding air and air gap were modelled with magnetic scalar potential. The solver sequence consists of the Coil Geometry Analysis, Stationary simulation and Time Dependent simulation. First of the magnetic flux densities of the air gap and on the surface of magnets from static simulations are compared with the analytic calculation approaches. The minor deviations between both approaches can be explained with the idealisations made for the analytic calculation. Since the FEM simulation is incorporating real flux paths and therefore field scattering or losses, FEM results are lower than the calculation approaches. Regarding the torque, 12Nm were set as the design benchmark for the analytic method. The simulated torque of a static simulation approach amounts to 10,79Nm due to less idealised constraints. For the comparison of phase EMF, measurements from test bench test runs were used, while EMF calculations were not finished at the time of abstract submission. Measurement and simulation results from the Time Dependent simulation show a very good concordance with a relative error of just 1,8%. Lastly phase inductivities measured align very well with we simulation results and Siemens Star-CCM Suite. Due to the non-linearity of the stator core material, a particular simulation sequence was set in place to obtain the phase inductivity values.
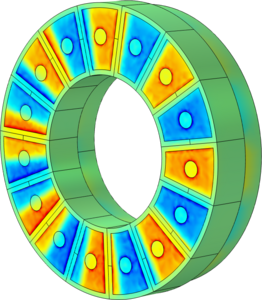