COMSOL® Modeling and Tensile Loading of Aluminum Material Test Samples
Material test samples are commonly subjected to tensile testing, with an extensometer used to measure changes in length of the material to determine strain. Lacking an extensometer, strain gages were used to measure longitudinal and transverse strain, with the location and magnitudes of strain guided by a COMSOL finite element model. Test samples were loaded with an Instron tensile test machine (model 5500R), and model strains were validated by comparison with measured strains in both the longitudinal and transverse directions for different aluminum alloys.
A three dimensional Solid Mechanics model was built, with the test sample profile geometry drawn using a CAD program (Ashlar-Vellum Graphite) and imported using the COMSOL CAD Import Module. The profile was extruded into a 3D bar and modeled as homogeneous, linearly elastic 6061 or 7075 aluminum. One end of each test sample was defined as a fixed constraint boundary. Loads were applied to the other end using a parametric sweep and keeping the material in its linearly elastic range (up to 2000lb for 6061 and 4000lb for 7075). An extra fine physics-controlled mesh was generated and a stationary analysis was performed using default solver settings.
Material test samples were fabricated from 6061 and 7075 aluminum bar stock and strain gages were mounted at the midpoint of the test section in the longitudinal and transverse directions. Strain gages were general purpose Vishay Micro-Measurements CEA-13-240UZ-120 and installed using standard techniques. Gages were wired as quarter-bridge Wheatstone circuits using a Vishay P3 Strain Indicator and Recorder. Loads were applied with the Instron test machine and longitudinal and transverse strains were recorded.
The figure below shows the first principal strain for 6061 aluminum with an applied load of 600lb. COMSOL model strain predictions were within +/-1.5% of measured strains. The test sample’s elastic modulus measured using a linear regression of all measured longitudinal stresses and strains (r2 = 0.9998) was found to be within 2% of literature values, and the Poisson ratio was within 2.5%. Similar results were found for the 7075 alloy test samples.
Despite its simplicity, this COMSOL model was useful in predicting and visualizing experimental stresses and strains, especially the stress concentrations between the grip regions at the test sample ends and the narrower test region. Model results guided placement of the strain gages. The model permits visualization of phenomena such as Saint-Venant’s principle, whereby the difference between the effects of two different but statically equivalent loads becomes very small at sufficiently large distances from the load *. This approach allows measurement of the elastic modulus and Poisson’s ratio for unknown material alloys. Close agreement between theory, model, and experiment validates the model, giving students confidence in this approach before moving on to more complex finite element models.
*A. J. C. B. Saint-Venant, 1855, Memoire sur la Torsion des Prismes, Mem. Divers Savants, 14, pp. 233–560.
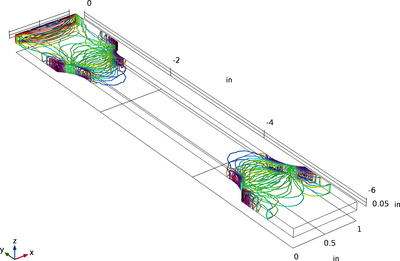
下载
- palladino_poster.pdf - 3.22MB
- palladino_paper.pdf - 1.36MB
- palladino_abstract.pdf - 0.05MB