3D Acoustic-Structure Interaction of Ultrasound in Fluids for the Manufacture of Graded Materials
Functionally graded materials (FGM) are those that contain chemical, phase or structural gradients. Whilst the design of functionally graded structures is well researched in areas such as shape optimisation and topology optimization, their manufacture is still in development. One potential method for manufacturing functional gradients within materials is the application of sonication, this is, pressure gradients produced by steady state ultrasonic acoustic fields applied to a metastable material that solidifies. The application of acoustic fields to the manufacture of graded materials offers exciting opportunities to produce truly 3-dimensional gradients. Understanding how this manufacturing process works requires an accurate model of fluid-structure interactions between oscillating ultrasonic transducers and an enclosed fluid.
In this paper the fluid-structure interaction of a fluid excited by ultrasonic waves in a purpose-built vessel is investigated. The work presents a validated 3-dimensional model for oscillating transducers generating a steady-state acoustic field in water. The model is then used to predict the resulting acoustic fields in a polymeric foam (i.e. metastable material) for a number of excitation frequencies and transducer configurations. The model was built in COMSOL Multiphysics® using the Solid Mechanics physics interface and the Pressure-Acoustics, Frequency Domain physics interface. A series of Acoustic-Structure boundaries were defined. The model geometry was designed based on a lab-scale rig used for investigating the interactions between ultrasound and a fluid. The mould dimensions were 132mm x 158mm x 120 mm and the walls had attachments for ultrasonic transducers. The model was able to simulate the operation of up to four transducers operating at a single oscillation frequency using a frequency domain study. In order to validate the model, water was used in the purpose-built rig to record experimental data. A Brüel Kjær 8103 hydrophone was used to measure the pressure at intervals of 2 mm to produce 1D plots of pressure in the fluid. The COMSOL Multiphysics® model was solved using water from the COMSOL Multiphysics® Material Library and compared to the acoustic pressure output from the hydrophone. The model was solved for a single and double transducer configurations oscillating at 25.3, 48.2 and 73.2 kHz. Following the validation with experimental data of water the COMSOL Multiphysics® Optimization Module was used to improve the accuracy of the model through a parameter estimation study. Three design variables were defined: (i) the power of the transducer, (ii) the stiffness of the external supports and (iii) the spring constant of a silicone sealant. These design variables were optimised to fit the experimental pressure measurements using the Nelder-Mead algorithm. Once the model is considered robust using water, a new material model will be explored in the Pressure Acoustics, Frequency Domain module for the polymeric foam (metastable material that solidifies) using the Poroacoustics model.
Good general agreement was seen on the spacing of the pressure nodes and antinodes for the oscillation frequencies of 25.3 and 48.2 kHz. The pressure magnitude was often inaccurate so the power of the transducer was the most significant design variable to be tested in the parameter estimation study.
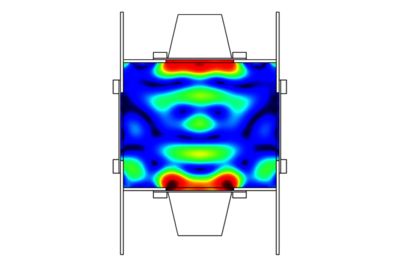
下载
- holt_presentation.pdf - 1.86MB
- holt_paper.pdf - 4.11MB
- holt_abstract.pdf - 0.03MB