A Multiphysics Model to Ensure Power Cables are Restrained Safely During Short Circuit Fault
Trefoil cable formation is used where three phases are carried by three single core power cables, rather than a single three phase multicore cable. The advantage of installing three single cores in such a configuration is that it minimises the induction of eddy currents, therefore reducing the effect of localised heating, while maintaining the current carrying capacity of the circuit. Trefoil cable restraining devices are structures used to hold the three single core power cables in a triangular touching (trefoil) formation, along the length of the laid cables. Short-circuit fault conditions of single core cables in trefoil formation result in high dynamic electromagnetic forces; these forces need to be restrained correctly in order to prevent extensive damage to the cable management system, and more importantly potential loss of human life. Manufacturers of trefoil cable restraining devices, or cleats, are required to physically test their product designs in an applied test, where a section of three single core power cables is held with cable restraining devices and exposed to a three phase short-circuit. Each assembly of cable restraining device, cable and applied current will yield a different result, so in theory, an infinite number of tests are required. These physical tests can be costly in terms of both expense and time. To assist the testing process, a time-dependent multiphysics model, including currents, induced electromagnetic forces, material plasticity and contact analysis has been developed to quickly assess various designs and implementation scenarios, greatly reducing the time and cost to asses, and quantify a trefoil cleat design during a short-circuit fault condition. The COMSOL Multiphysics® model developed was validated against physical tests for a number of cleat designs, materials, and attachment configurations, and compared to empirical solutions.
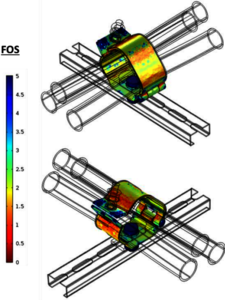
下载
- yeoman_presentation.pdf - 4.54MB
- yeoman_poster.pdf - 1.22MB
- yeoman_paper.pdf - 1.12MB
- yeoman_abstract.pdf - 0.01MB