Analysis of Stress, Strain, and Deformation in PALF/MMA Composite Materials in COMSOL Multiphysics
The complexities of prosthetic challenges require detailed and specific design solutions that correspond with all aspects of the challenge [1]. Most pragmatic prosthetic design solutions consist of components with elaborate three-dimensional geometry designed with materials with unique behaviour [2], [3]. The intricacies of designing effective engineering solutions make manual approaches challenging and inefficient. For efficiency in product design and development, these challenges are best modelled numerically and solved by computer simulations such as the finite element method [4]. Furthermore, the complex nature of most prosthetic solutions makes it time-consuming, costly and risky to design prototypes and conduct experimental tests, especially on patients. However, computational methods such as the finite element analysis in COMSOL Multiphysics® v. 6.0 make it possible to design, test, evaluate and improve prosthetic solutions, irrespective of their complexity and at minimal risk [5]. This paper presents findings on the stress, strain, and deformation behaviour of a transtibial prosthetic socket (PS). A 3D model of the PS was assigned with the material properties of a new PINE-composite and then subjected to static structural analysis [6]. The analysis involved applying a pressure of 9230 Pa to the internal surface of the PS and studying the stress, strain, and deformation behaviours. It was found that the highest stresses occurred at the distal end of the socket, which was fixed during the simulation and represents the stress concentration point where the PS is connected to the pylon through the socket adaptor. Similarly, the peak strains were also located at the distal end, but the total deformation of the PS was concentrated at the proximal lateral and medial ends of the socket. The peak stress and strain values recorded during the simulation were below the experimental yield stress and yield strain of the PINE-composite material model. This indicates that the material properties used in the simulation can handle the estimated maximum pressure (9230 Pa) of an amputee with an approximate body mass of 122 kg.
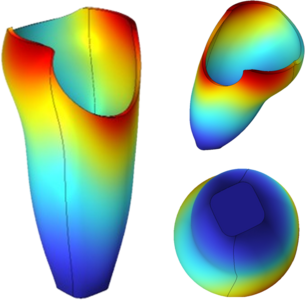
下载
- gaba_11141_poster.pdf - 0.44MB
- 3_eric-gaba.pdf - 0.97MB