Design Criteria of the Passive Joints in Underactuated Modular Soft Hands
The diffusion of underactuated compliant hands is growing in the robotic community due to their robustness, adaptability, capability of exploiting environmental constraints while performing a task, availability and low cost. In particular the interaction with the environment and the simplification of the control is a central aspect in the design of the device.
In this paper we exploit the design of passive joints in underactuated robotic hands and in particular the role of joint stiffness in the definition of fingertip trajectory, grasp forces applied to object, and overall grasp stiffness.
In this work we mainly focus on passively compliant hands composed of deformable joints and rigid links, actuated with a tendon for each finger, connecting all the rigid links. First we define a set of criteria and suitable procedures for the evaluation of the values of passive joint stiffness.
In our previous works we considered as main criterion the assignment of hand fingertip trajectories: passive joint stiffness values were defined so that the fingertips of the robotic hand followed the trajectory that human hand fingers mainly follow when they freely move while approaching to an object to be grasped (first postural synergy). This criterion is useful to define the way the robotic hand is going to approach to an object: in our preliminary tests we observed that following this methodology a higher number of objects are reliably and efficiently grasped with respect to a hand in which passive joint stiffness are not optimized and are set equal for all the joints. In this paper we will go deeper in this analysis and we will consider other interesting criteria, which more in detail look at the interaction with an object and external surfaces.
The second aspect that will be considered deals with passive joint structural design: once stiffness values have been determined, methods for defining passive joints shape, dimension and material have to be defined. These components are realized with additive manufacturing techniques, using materials whose properties are highly variable and nonlinear: in this phase we are going to use COMSOL Multiphysics® software. FEM structural simulation will allow to optimize geometrical and material parameters of passive joint to accomplish with the results of the specific optimization criteria. Results will be validated with experimental tests performed with a prototype. We furthermore are going to extend this methodology to continuous soft hands: in this framework the role of FEM simulation will be either more significant.
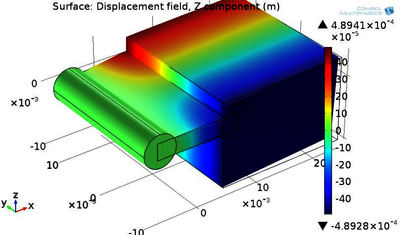
下载
- malvezzi_poster.pdf - 0.68MB
- malvezzi_paper.pdf - 7.37MB
- malvezzi_abstract.pdf - 0.87MB