Electric Field Assisted Formation of Polymeric Hollow Microstructures
Hollow microstructures find numerous applications in microsystems, bioMEMS and microfluidic systems [1]. Consequently, one-step fabrication process of hollow polymeric microstructures by external electric field along with capillary forces, termed as electric field- assisted capillarity (EFAC), has attracted the attention of researchers over conventional methods [2]. Localized higher voltage due to heterogeneous electric field over the thin film makes the polymer grow upward and due to capillary forces it flows encapsulating the inner electrode, as shown in Figure 1. This study focuses on understanding various important parameters involved in fabrication of encapsulated hollow polymeric microstructures by EFAC by developing a multiphysics computational model. Use of COMSOL Multiphysics®: A 2D transient model is developed for Newtonian polymer film which is assumed to be infinite in the third dimension. Figure 2 shows the details of computational domain along with the applied boundary conditions. Meshing was done using Physics-controlled Fine mesh. Electrostatics (es) Interface and Laminar two phase flow phase field interface are used. In Electrostatics (es) Interface, Electric field is solved using the Laplace’s equation for the voltage. Laminar two phase flow phase field Interface solves the incompressible Navier–Stokes equation using phase field method. Phase field method was selected instead of level set method in COMSOL as there is no mass conservation in level set method. It can be seen from Figure 3 that instabilities in the film appear faster as the applied electric field is increased and it encapsulates the electrode rapidly. This knowledge steers to a novel concept that by applying a linearly increasing voltage, a hollow structure can be fabricated with desired thickness at the top, as shown in Figure 4. In conventional fabrication techniques, this type of controlled hollow structure fabrication is comparatively time consuming and require special skills with multiple steps. The outcome of parametric studies provides significant insights into a new fabrication technique for manufacturing of encapsulated hollow polymeric microstructures of controlled thickness using electric field-assisted capillary action.
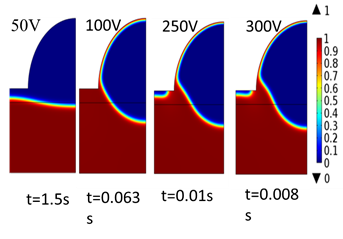
下载
- atta_presentation.pdf - 0.86MB
- atta_paper.pdf - 0.77MB
- atta_abstract.pdf - 0.15MB