Level-Set based Topology Optimisation of Convectively Cooled Heatsinks
Introduction Thermal management is a key challenge in development of modern microelectronics systems. This is becoming an increasingly critical area of microelectronics packaging design due to the ever increasing levels of miniaturisation, integration and operating frequency which result in significantly higher power densities. This study looks to address this challenge through advanced topological optimisation techniques using the COMSOL Multiphysics® analysis framework. This study uses a Level Set (LS) based Topology Optimisation (TO) approach to maximise the thermal performance of 2D and 3D heatsink designs. Multi-objective optimisation of a thermal compliance/viscous dissipation problem is additionally performed.
Numerical model The LS optimisation process is iterative in nature. After initialisation of the LS distribution, iterative steps (comprising; i) solution of the fluid flow and heat transfer physics ii) evaluation of shape sensitivity iii) evolution of the LS) are repeated until the objective reaches a minimum and area constraints are satisfied. As the iterative procedure progresses, the LS gradient may become excessive, leading to a degradation in accuracy and stability. LS re-initialisation is performed at regular intervals in order to mitigate against this. Multiphysics fluid flow and heat transfer are analysed using COMSOL Multiphysics®, with level sets evolved through the solution of Hamilton Jacobi’s equation using an upwind Finite Difference method implemented in MATLAB®. Shape sensitivity is calculated in COMSOL Multiphysics® and coupled to MATLAB® through Livelink™ for MATLAB®.
Results A typical microelectronics thermal management problem has been assessed to demonstrate the approach. An active semiconductor device is subject to a convective cooling air flow. A volume surrounding the device can be used to accommodate a heatsink. The LS TO approach is used to define the shape of this heatsink which will result in a minimal device temperature. A device heat flux of 700W/m2 and an inlet Reynolds number of 600 are defined. Symmetry is exploited to allow one half of the domain to be considered. Numerical domain is rectangular in shape with flow inlet at top and heat source at bottom corner. The optimisation is performed for two material types, expressed simply as fluid-solid thermal conductivity ratios (Kf/Ks=0.001 & Kf/Ks=0.1). The optimised shapes both exhibit the expected tree-like shape with a solid base in the vicinity of the semiconductor device and increasingly fine dendrite/branch structures toward the domain borders.
Conclusions The direct conclusions arising from this study are that heat sink designs applicable to the microelectronics industry can be optimised through adoption of a LS TO analysis approach. The broader implications are more profound in that numerical optimisation approaches can be used to optimise designs considering an array of physical phenomena. As such, this leads the way to increasing adoption of autonomous design wherein an engineer sets constraints and allows algorithms to determine an optimal design.
COMSOL Multiphysics® is a registered trademark of COMSOL AB COMSOL® is a registered trademark of COMSOL AB Livelink™ is a trademark of COMSOL AB MATLAB® is a registered trademark of The MathWorks, Inc.
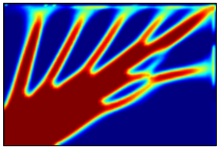
下载
- santhanakrishnan_presentation.pdf - 2.79MB
- santhanakrishnan_paper.pdf - 1.91MB
- santhanakrishnan_abstract.pdf - 0.04MB