Multibody Dynamics Analysis of a High Speed Metal Forming Press
The COMSOL Multiphysics® Multibody Dynamics Module was used to analyze the performance of a high-speed metal forming press consisting of multiple processes for preform of aluminum blanks. The objective was to redesign the drive mechanism of the press, changing from a 4 bar linkage mechanism to a hypocycloidal gear system. The redesign aimed to increase the machine operating speed by 40% while at the same time eliminating any vibration associated with the original 4 bar linkage system.
A detailed CAD containing all the different parts of the new drive mechanism was imported into COMSOL Multiphysics® using the CAD Import Module. Materials were then assigned to the different parts of the mechanism. Using the Multibody Dynamics interface, rigid bodies were assigned to all parts of the mechanism. The gears were modeled as rigid bodies using the spur gear domain and assigning number of teeth, pitch diameter and pressure angle. The connections between the different mechanism parts were established through the use of Joints from the Multibody dynamics interface. The type of Joints used for the model set up were Fixed Joints and Hinge Joints. The connections between the gears were defined through the use of Gear Pairs. The generated gear torque was calculated through computing the contact force acting on the teeth. An initial rotational speed was assigned to the flywheel of the mechanism through the use of prescribed angular velocity.
The Multibody Dynamics analyses aimed to obtain the torques generated in the different gears during the machine operation under different load case scenarios of the process. The aim was to extract the generated gear torques in order to use them for detailed stress and fatigue analyses on the gears. The analyses were also used to calculate the level of loads acting on the shafts and bearings. This allowed the team to establish the appropriate type of bearings for particular process loads.
The initial mechanism analysis identified high torques on the gears, and as a result, several design iterations of the mechanism were conducted to reduce the generated gear torques and improve the fatigue life of the gears. The dynamics of the system were identified through the use of COMSOL Multiphysics® Multibody Dynamics Module and by changing the masses of critical parts of the mechanism the effect of process loads on the generated torques was minimized. As a result, the level of torques on the gears was reduced and the gear safety factors were increased. Moreover, the model identified very high loads in one of the shafts where the initially selected bearing would have not withstood those loads. As a result, the type and size of the bearings were changed in order to account for those high loads. Overall, the use of the Multibody Dynamics analysis enabled the identification of risks at the early design stage which allowed to take appropriate actions and mitigate those risks.
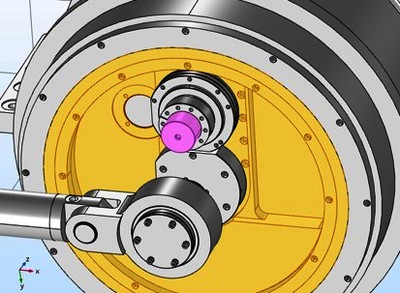
下载
- Redriven-Comsol_Conference_v1.0.pptx - 0.83MB