Numerical Modelling and Validation of Induction Melting of IN713C for Investment Casting
Investment casting is practised in both the automotive and aerospace industries, to produce casted components where a high-quality surface finish is critical. Vacuum induction melting (VIM) and direct pouring into an investment casting shell mould is an advantageous manufacturing technique, due to the speed at which casting trees with a high yield can be produced. However, variables introduced in the VIM process can affect the resultant temperature and velocity profiles of the alloy during induction heating, melting and subsequent pouring. An understanding of induction heating and melting is invaluable in determining the effect of these variables upon the quality of the finished castings. Numerical modelling of the induction heating and melting process is vital in developing this understanding.
Data on measured temperatures of an Inconel 713C (IN713C) billet in a small-scale induction melting experiment during heating and cooling cycles were recorded using an optical pyrometer. The billet was heated and melted using an induction coil, followed by cooling as the coil power was switched off. This cycle was repeated, with heating and cooling curves plotted with respect to time.
The ability to accurately model the heating, melting, and cooling of an IN713C billet on a smaller scale, provides a solid foundation for modelling VIM investment casting on a larger industrial scale. Development of an experimentally validated, accurate induction melting model paves the way to a greater understanding of the VIM process for the application of component production in the automotive and aerospace industries. Principles from the model can be applied to a larger scale model, providing an effective tool to investigate the effect of variables such as alloy condition on the quality and yield of finished castings.
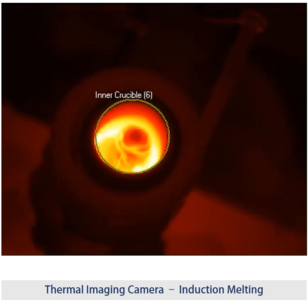
下载
- comsolpaper.pdf - 1.62MB