Numerical Optimization of the Ultrasonic Cleaning Technique for Pipelines
Fouling accumulation in pipelines is a known problem in industry which is currently treated by mechanical, hydraulic and chemical means. Each requiring a halt in the production to carry out the procedure. Industry requires a method that is non-invasive and can be used in-situ, Ultrasonic cleaning has been proven to be an effective technology for fouling removal but which requires optimization of power, frequency, waveform and topology. A numerical methodology is created in COMSOL Multiphysics®, utilizing the Solid Mechanics, Electrostatics and Pressure Acoustics interfaces to portray the sonication from the 40 kHz cleaning transducer into the pipeline structure which is filled with liquid.
The model focuses on a stainless steel pipe filled with water (stationary) and a bespoke high power ultrasonic cleaning transducer is attached to the outer wall. The initial model has shown good correlation to the cleaning patterns achieved within laboratory investigation as well as achieving a minimum of 5 Bar of pressure within the fluid, which corresponds to the minimum threshold necessary to generate cavitation in a liquid. The methodology is applied to a Schedule 40, 6-inch diameter, 6-meter long, carbon steel pipeline for further optimization of the technique, which has shown potential improvements of the sonication by means of an ultrasonic transducer array, achieving long-distance wave propagation and cleaning. This method has shown prospects of optimizing an ultrasonic cleaning solution for a given structure.
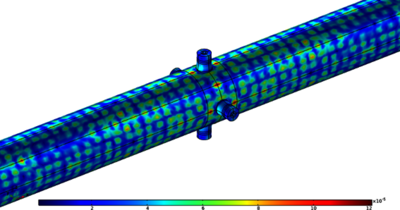