Selectively Permeable Membrane Gas Separation System – Modeling and dNN Tool Development
The Triton team was contracted to model and optimize a gas separation/pre-concentrator system involving selectively permeable membranes. The system would nominally include an input of mixed gas species at some driving pressure, a number of membrane modules, and separate permeate/retentate outlets, with a goal of providing a permeate gas stream with significantly higher concentration of a target gas species than in the incoming feed stream. Parameters of interest for overall performance study included membrane properties, feed stream pressure and flow rate, feed stream composition, and geometric configuration of the membrane module.
The evolution of the COMSOL model for this effort began with high-fidelity 2D model that included a representative cross-section of the feed, membrane, and permeate domains. Concentrated gas species transport was modeled in the feed domain (primarily convective) and permeate domain (diffusive and convective due to Stefan velocity), and was coupled to selective diffusion into, through, and out of the solid polymer membrane domain based on membrane properties and local gas species partial pressures. Over time, appropriate correlations and simplifications were identified and incorporated into updated versions of the model after comparable results could be obtained – e.g., the explicitly meshed membrane domain was replaced by transport equations that compared variables on either corresponding side to specify local species fluxes (with similar results obtained from both methods, the latter being significantly faster and less resource-intensive). Eventually, a cross-flow, spiral-wound configuration was approximated using a 2D geometry with multiple distinct but coupled fluid flow and species transport physics, with membrane flux implemented as spatially-varying out-of-plane flux.
FEA model results were validated against calculations of a well-mixed membrane separation model and found to be consistently similar, less some factor to account for geometric effects.
With the release of COMSOL 6.2 and its built-in Deep Neural Network tools, it was found that the model had been optimized enough for runtime and performance evaluation that a surrogate model tool could be generated. Thousands of simulation runs were completed across a span of parameters of interest (primarily membrane selectivity and inlet mass flow rate), generating estimates for permeate composition and module performance. Neural network models were trained on this data and used to create critical design curves (forward, performance as a function of given system properties) and iso-performance curves (inverse, required properties as a function of desired performance) for the system. These results were then combined with a catalog of hardware performance to aid in the selection of system components (e.g., compressor, module bay size).
COMSOL modules utilized in this workflow include the CFD and Chemistry add-ons. As of this submission, the Triton team has proposed the use of the COMSOL Compiler to create a stand-alone system optimization tool for the customer (to be built in the COMSOL Application Editor) and has received positive feedback. It is anticipated that future work will include additional performance mapping against currently fixed parameters (e.g., geometry, driving pressure, gas composition, temperature) and integration of these results into the performance estimation models and stand-alone application.
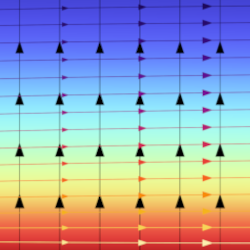