Simulation of the Additive Process of Forming 3D Products from HSLA Steel 09G2S
The results of modeling of thermal fields, stresses, deformations and displacements in formation of an additive structure from structural low alloy steel for welding 09G2S on a substrate are presented. An interdisciplinary research computational package COMSOL Multiphysics® was used for computer modeling. Effect of temperature on physicochemical parameters of steel was taken into account in the work. The results for modeling were obtained using Gleeble 3800, a complex for simulation of thermal deformation state of welding thermal cycle. Some physical-thermal properties of 09G2S steel were calculated using JmatPro® 6.0 software package. Carried investigation showed that the highest level of residual stresses and deformations in the additive deposition of 09G2S steel layers on the substrate is reached at the boundary of the first layer and substrate and makes 280 - 320 MPa. Stresses between the layers of deposited metal are significantly lower (to 50 MPa). It is determined that increasing the number of deposited layers provokes a nonlinear rise of a level of stress at the additive layer / substrate boundary and does not depend on the number of deposited layers in time. In additive manufacturing process, preheating to at least 300 ... 320 °C should be used to prevent noticeable deformation of the substrate. Developed software can be used for mathematical modeling of additive process of formation of steel, titanium and aluminum alloys structures.
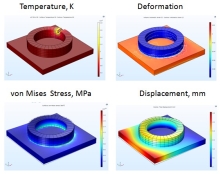
下载
- kostin_poster.pdf - 0.51MB
- kostin_paper.pdf - 1.99MB
- kostin_abstract.pdf - 0.05MB
- download (1).jpg - 0.03MB