Topology Optimization of an Actively Cooled Electronics Section for Downhole Tools
INTRODUCTION: Active cooling systems represent a possible solution to the electronics overheating that occurs in downhole tools operating on wireline, a cabling technology used to remotely control the downhole devices during oil and gas well interventions, in high temperature wells (150 ⁰C < T < 200 ⁰C) [1]. The integration of a thermoelectric cooler (TEC) into a downhole tool electronics section was studied [2], so the temperature-sensitive electronics could be maintained at a tolerable temperature, below the well temperature. The space constraints and the variety of power-dissipating components make the integration of the TEC challenging: the cooling zone is very close to the heat sink and to other heat sources, and a good performance of the system relies both on a good heat rejection path from the cooler to the well and on a good insulation of the cooled electronics.
USE OF COMSOL MULTIPHYSICS®: A 3D model of the system (Figure 1) was built in COMSOL Multiphysics® software; the topology optimization approach (Solid Isotropic Material with Penalization) [3] [4] was adopted, in order to define a thermal management strategy that minimized the temperature of the temperature-sensitive electronics and optimized the distribution of thermally conductive material and thermal insulation inside the electronics unit. The heat transfer within the system was simulated using the Heat Transfer Module: volumetric and boundary heat sources reproduced the electronics power dissipation, thin resistive layers simulated the contact thermal resistances and a convective heat flux represented the interaction between the tool and the well fluid. The TEC was modelled with a modified heat transfer equation, implemented through the Coefficient Form PDE interface, which accounted for the thermoelectric effect that drives the cooling process. Thermoelectric properties were based on measured properties for Bi2Te3 and are temperature dependent. A density filter [5] was implemented through the Coefficient Form PDE interface, in order to avoid mesh-dependent solutions, and coupled with a projection function [6], in order to obtain a better resolution of the design variable distribution. The Optimization Module was used to define the objective function, the design variable and its constraints. The method of moving asymptotes (MMA) was then used to solve the topology optimization problem.
RESULTS: Using the COMSOL LiveLink™ for MATLAB®, the topology of the electronics unit was optimized for several boundary conditions of TEC feed current and external well fluid convection. Different boundary conditions generated different optimized designs: low TEC feed currents and high heat transfer convective coefficients led to designs where the thermal protection of the cooled electronics is prioritized (Figure 2); high feed currents and low convective coefficients produced designs where the use of thermally conductive material is preferred, so the heat rejection to the well is enhanced (Figure 3).
CONCLUSIONS: The optimized topologies were analyzed, compared and their robustness evaluated. According to the simulation results and to the design constraints, an actively cooled downhole electronics unit prototype was designed. The topology optimization approach proved to be a powerful technique that can support the design of new products and meet the designer’s needs.
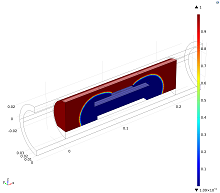
下载
- soprani_presentation.pdf - 1.9MB
- soprani_paper.pdf - 1.11MB
- soprani_abstract.pdf - 1.6MB