Wire Bonding: A Thorough Numerical Methodology
The semiconductor industry is always looking for early anticipation of manufacturing risk, pushing the development of Computer Aided Engineering (CAE) modeling of processes. Robust Chip-Package Interaction requires a deep understanding of thermo-mechanical stresses imposed during the assembly process; one of the critical steps is wire bonding, which can damage pads inducing cracks.
Aim of this paper is the investigation of an appropriate simulation strategy, using the COMSOL Multiphysics® software, of a 3D thermo-mechanical model of thermo-sonic wire bonding, that represents the physics accurately by a robust numerical approach. The usage of simulation together with experimental data to obtain mechanical material characterization for small diameter copper wires at high temperature is also shown.
First step is the implementation of a parametric 2D axisymmetric model with rigid capillary and pad, allowing to focus on the set up and copper wire characterization. Functionalities from the Structural Mechanics module are used: hyperplastic constitutive law with plasticity is used for describing copper behavior at high temperature; contacts are imposed (capillary-ball and ball-pad). Displacement controlled and force controlled capillary movement is studied. Matching both the experimental imposed force and vertical displacement on the capillary is used as a strategy to characterize material for the copper free air ball (FAB) at high temperature. This strategy is valid for experiments with and without acoustic softening. Imposing force or displacement results in predicting slightly different properties for the FAB. This discrepancy is imputed to a too simplistic description of the capillary movement, since there is no information available on its inertia or damping. A transient simulation seems to more accurately, but not perfectly, capture the experimental behavior.
A robust model set up is also sought for transient and 3D analysis. If the physics contains inertial terms, there is no need for spring foundations. On the other hand, material damping information would be needed to build a physically sound model. Since no information on material damping is available the BDF time stepping solver is used, instead of the default generalized alpha, to introduce numerical damping. The construction of a more robust model will speed up our future investigation of the wire bonding process. Further enhancements could be modeling ball/pad soldering process and, when acoustic softening is present, imposing a force instead of displacement to control the horizontal capillary movement.
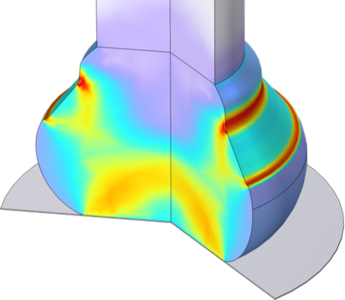