Analysis of Mixing Chambers for the Processing of Two-Component Adhesives for Transport Applications
Two-component adhesives are commonly used for sealing and joining in transport applications for mechanically highly stressed connections. At the Chemnitz University of Technology an innovative system technology for the user-friendly, wireless and energy-efficient processing of two-component adhesives with electrical drive is developed. In this context, the simulation-based layout of main components for the achievement of high mixing rates as well as the minimization of pressure losses are key challenges. For an electrically-based mixing system for two-component adhesives, a high mixing intensity and a low energy demand are required. In the present study a fluid-dynamic simulation model of a pre-mixing chamber with two inlets for the two adhesive components was established. Mass transport equations for the calculation of the phase distributions were implemented and evaluated with regard to calculation effort and information content. Further assessments of the results was realized by using different parameters characterizing the phase distribution and the hydraulic power demand. The conducted simulations with COMSOL Multiphysics® led to a better understanding of the flow behaviour in the pre-mixing chamber for the two adhesive components in particular in the area of the accelerator component injection (Fig. 1). With the simulation results a suitable design for this inlet geometry could be identified. The evaluation of the mixing parameter revealed the result, that fluid-dynamical behaviour and phase distribution are influenced by the inlet diameter of the accelerator component due to changing fluid-dynamics effects. Concerning the power demand of the fluid technical system it was determined that the non-newtonian viscosities of the adhesive components are essential factors.
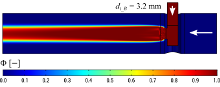
下载
- schaarschmidt_poster.pdf - 1.3MB
- schaarschmidt_paper.pdf - 0.62MB
- schaarschmidt_abstract.pdf - 0.03MB