CFD Analysis of a Stirred Vessel Bioreactor with Double Pitch Blade and Rushton Type Impellers
Stirred tank bioreactors are used to simulate a natural biochemical environment for the optimum growth of cells (i.e. algae, microorganisms or tissues) in microbial and cell culture. Bioreactor types range from small (5 L and less) up to 15000 L systems for large-scale industrial applications. Regarding the purpose they can be batch, fed-batch or continuous flow. Tight control over parameters such as temperature, pressure, pH, oxygen and stirring rate will produce the most desired results - maximized cell growth and biomass production which often has a high added value. Magnetic coupling impellers are used with-in the fermentation industry where increased demand for sterilization is a must. A magnetic coupling is a coupling that transfers torque from shaft using a magnetic field rather than a mechanical connection. This set up is also used for ease of maintenance. In order to gain better understanding how the cells might be affected by the choice of impellers, rotational speeds and consequent shear rates, tank geometry and magnetic field the CFD (Computational Fluid Dynamics) analysis was set up using COMSOL Multiphysics® software. For this aim a customized COMSOL Multiphysics® Mixer model was used from the CFD module's Application Library. Velocity, pressure and wall resolution profiles of the system were studied. In addition to the above profiles the following plots were also added: eddy diffusivity, shear rate, power number vs Reynolds number, shaft power and torque vs rpm (revolutions per minute). The reactor construction was a dish bottom with three baffles and two types of double impellers (Rushton and pitched blade). Each configuration was simulated at a range of revolution speeds i.e. 100-1000 rpm with 100 rpm step. Three vertical slices were implemented through the whole diameter of the reactor in the YZ plane which displays results of velocity dynamics. In the double Rushton impeller system (Figure 1) velocity and shear rate close to the impeller blades is higher than near the walls. Use of baffles prevent the vortex formation in the center of reactor and contribute to better mixing. The simulation results are in reasonable agreement with observation and theory, however more work has to be done to refine the current model. The ongoing study of our research is to investigate how the reactor scale-up would affect the key variables such as Reynolds number, shaft speed and power to volume ratio in 1000 L, 4000 L and 15000 L reactor systems. A comprehensive set of simulation profiles were obtained including velocity, pressure and wall resolution using CFD. The main purpose of this research is to understand: how different reactor parameters might affect the key process variables (i.e. shear rate, velocity) that are critical for optimum biomass production.
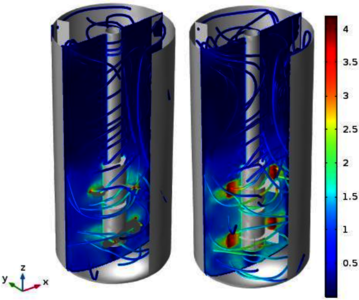
下载
- buss_poster.pdf - 2.78MB
- buss_paper.pdf - 1MB
- buss_abstract.pdf - 0.15MB