CFD Modeling of a Mixture Device for Medical Applications
INTRODUCTION This work investigates flow characteristics in pipes and its utilization for a mixing process. The influence of swirl flow on the mixture is of particular interest. There are several studies, which examine the relationship between swirl flow in pipes and heat transfer, such as the recent study in [1]. In addition to this, swirling pipe flow has been investigated with regard to its decay [2]. The model described here is built up to study a particular mixing device for medical applications.
USE OF COMSOL Multiphysics® Suitable, simplified simulation geometries are obtained by splitting the device in varies pipe branches with different sizes. The geometry of the simulation model is build up as a Y junction with variable dimensions to study different types of fluid flow. Besides the flow characteristics, the impact of the geometric parameters is investigated with parametric sweeps studies. Using varies laminar and turbulent physics interfaces of the COMSOL Multiphysics® CFD Module, the model is used for stationary studies. Material properties of water are used in the model. To specify the inlet velocity, two spherical coordinate systems are defined at both inlet boundaries. Using the in-plane coordinate φ, it is possible to define inlet flow with an angular momentum. The influence of swirl on the resulting outlet flow has been investigated by varying the ratio between the axial flow and the radial flow component. For solving the high velocity gradient near the walls, a hybrid mesh is used, which consists of a free tetrahedral mesh and a boundary layer mesh.
RESULTS The simulation provides three main results. First, streams with a concordant angular momentum on both inlets result in a stream with an angular momentum at the outlet. This is not true if the angular momentum at the inlets are in the opposite directions. Secondly, the study of swirl flow at the inlets has shown a significant influence on the mixture. In comparison to axial flow at the inlets, swirl flow leads to a higher mixture ratio as exemplified shown in Fig. 1. Therefore, streamlines starting at both inlets have been evaluated at the outlet. Thirdly, the influence of the mixture chamber has been investigated. For this purpose two additional CFD models have been built up. One with a spherical mixture chamber and one with an ellipsoid. The simulation results provide insight to the impact of the chamber geometry on the mixing quality.
REFERENCES [1] K. M. Saqr, A. I. Shehata, A. A. Taha, and M. M. Abo ElAzm, “CFD modelling of entropy generation in turbulent pipe flow: Effects of temperature difference and swirl intensity,” Applied Thermal Engineering, vol. 100, pp. 999–1006, 2016. [2] H. A. Vaidya et al., “Numerical simulations of swirling pipe flows- decay of swirl and occurrence of vortex structures,” J. Phys.: Conf. Ser., vol. 318, no. 6, p. 62022, 2011.
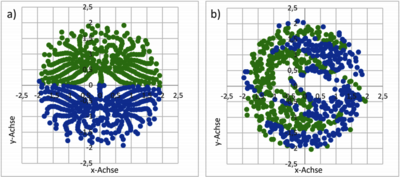
下载
- sandkühler_poster.pdf - 0.78MB
- sandkühler_abstract.pdf - 0.29MB