Constitutive Modeling of Polyethylene in COMSOL Multiphysics® Software
Introduction The constitutive behavior of Polyethylene, like most polymers, is nonlinear, temperature, and strain-rate dependent. It cannot be accurately represented with standard elastic-plastic or hyperelastic material models [1]. The focus of this work is on Medium Density Polyethylene (MDPE) due to its widespread used in the gas pipe industry.
We selected a material model that employs two parallel rheological networks (see Figure 1): a hyperelastic Mooney-Rivlin element (Network A) and a Mooney-Rivlin element in series with a nonlinear power-law flow damper (Network B). We used a large strain formulation where the deformation gradient of Network B is formulated as the product of elastic and inelastic deformation tensors. We used temperature dependent scaling factors to modify the Mooney-Rivlin constants and the flow resistance. More advanced material models suitable for polyethylene are available in the PolyUMod library [2]. This relatively simple model framework however provides a reasonable fit to experimental data in order to focus on the implementation details.
Uniaxial tension and compression tests were performed on MDPE samples, reaching high strains, at several temperatures and strain rates. The tests included loading/unloading cycles at different strain rates and several hold segments to allow for stress relaxation. The tests were performed by the Gas Technology Institute (Des Plaines, Illinois); we calculated the values of the material model parameters that best fit their experimental data. Figures 2 and 3 show some of the experimental data and the corresponding material model predictions. Figure 2 is for cyclic compression tests at three temperatures, and Figure 3 is for uniaxial tension at three strain rates. The model predictions are in good overall agreement with the experimental data.
Use of COMSOL Multiphysics® We implemented this material model in COMSOL Multiphysics® software using coupled ordinary differential equations (ODEs). This unique COMSOL functionality enables the solution of custom differential and/or algebraic equations. We modeled Network A using built-in hyperelastic material models in COMSOL software with no modifications. For Network B we explicitly provided the hyperelastic equations, including the weak form, as a function of the elastic component of the deformation gradient. We used the components of the inverse of the inelastic deformation gradient as independent variables.
We verified the material model implementation by simulating several virtual experiments using COMSOL software. In all simulated cases the model matched the predictions of our material calibration software, MCalibration®. Figure 4 shows the model predictions for a cyclic uniaxial tension test. The calibrated material model was used by the Gas Technology Institute for simulation of squeeze-off of gas pressure pipes [3].
Conclusions We implemented a material model that captures the large strain behavior of MDPE in COMSOL Multiphysics using the ODE functionality. The same approach can be used to implement material models for other elastomers, thermoplastics, thermosets, and foams. We calibrated the material model to experimental compression and tension data, and verified the implementation by simulating several virtual test cases. COMSOL Multiphysics provided the ideal environment for developing new material models, as well as simplifying the model verification process.
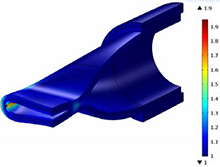
下载
- elabbasi_presentation.pdf - 0.87MB
- elabbasi_abstract.pdf - 0.02MB