Design and Fabrication of Small-Scale Supersonic Wind Tunnel
Introduction:
A small-scale supersonic wind tunnel can represent a convenient platform for supersonic flow testing. The scale considered in this work, with maximum cross-sectional area of 1”x1”, requires simpler structure in addition to the low budget costs and minor space requirements. While the small size tunnel may limit the data acquisition capabilities, it still makes it possible to construct the tunnel with limited space and resources. This tunnel will be part of the thermo-fluid laboratory (TFL) at Vaughn College and intended to be used primarily for educational purposes.
The tunnel, which is modeled using CATIA, (shown in figure 1) is being designed to generate air flow at 1.5 Mach number in the testing section. The tunnel consists of four sections. The sections in the flow direction are 1. Small size reservoir to operate at 70 psi pressure and standard atmospheric temperature. 2. A convergent-divergent nozzle to accelerate the flow to the desired speed. 3. The testing section with constant cross-section area of 1”x1” and a transparent side window for flow view access. 4.A diffuser section to slow down the flow at the tunnel exit. The m
Use of COMSOL Multiphysics® Simulation Software:
The design process heavily utilizes CFD analysis using the COMSOL Multiphysics® software's High Mach Number Flow physics. Several iterations are implemented to ensure reaching the desired Mach number at the testing section in addition to slowing down the flow speed at the tunnel exit. The use of COMSOL Multiphysics® has been essential to finalize the tunnel dimensions. The simulation is also used to determine the resulting force acting on the tunnel structure due to the flow motion.
Results:
The supersonic wind tunnel dimensions are determined based on the CFD analysis using High Mach Number Flow simulations in the COMSOL Multiphysics® software. The analyses are done using transient and stationary studies for the imported 3D model. The solution convergence of the stationary study was not obtained in higher mesh density cases compared to the transient studies which were achievable in similar cases. The Mach number of the final analysis is shown in figure 2.
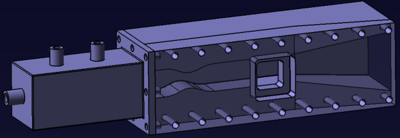
下载
- arteaga_poster.pdf - 1.42MB
- arteaga_paper.pdf - 1.36MB
- arteaga_cfdfsi_presentation.pdf - 3.29MB