Electrostatic Modelling of a Particle Application Module for Additive Manufacturing
The next step in the evolution of the metal sector of Additive Manufacturing and especially for Laser based Powder Bed Fusion is the production of multi-material components as shown by [1]. Therefore, the powder application module must be able to selectively arrange different powders in each subsequent layer. There is great potential to this end in the field of electrostatics. Powder can be transported to the application by electrostatic fields via Coulomb forces. The basic system can be modeled with an RC network, as it is the case in the analog process of electrophotography [2]. However, material data, permittivity and electric conductivity are required to calculate the lumped parameters of the system. Unfortunately, precise material data are not available. This paper describes the procedure to extract the required material data by using measurement data in combination with a two-step finite element model approach.
The model setup is based on the COMSOL® Electrostatics interface. The underlying 3D mesh is defined by the surrounding air and geometries as well as the insulating film which is a stack of layers containing an organic photoconductor (OPC) on the outer layer. Symmetric conditions are set with Zero Charge boundary conditions as well as Infinite Element Domains to reduce mesh size. A User-controlled mesh is set up to model the insulating film either through various film layers (10-100 µm) or one bulk layer followed by a mesh refinement study for numeric precision and efficiency. A first model (1) replicates a capacitance measurement setup in which the insulating film separates two aluminum electrodes. A Terminal and a Ground boundary condition are applied to the electrode domains and boundaries respectively.
Model (2) replicates the setup for electrostatic powder processing. Here, the applied surface charge on the OPC layer decays over time because of the electrical conductivity of the insulating layer composition. Experiments were conducted to measure the decay characteristic. The results are implemented by an Analytic Function linked to a Terminal boundary condition. To model the electrostatic field, another Terminal boundary condition is set to simulate the DC offset for powder attraction.
The permittivity is varied in model (1) by a Parametric Sweep until the measured and simulated capacitance coincide. A permittivity of 3.38 was found. The result is consistent with values obtained from analytical calculations. Various layer compositions of the isolator film are investigated with a Parametric Sweep for permittivity and thickness. This enables customized OPC films in future development. The permittivity is applied for model (2) to determine the capacitance and to evaluate the powder attraction capabilities with respect to temporal and geometric dependencies. Therefore, distance and potential parameters are varied via a Parametric Sweep in a Time Dependent Study.
[1] C. Anstaett, C. Seidel & G. Reinhart, Fabrication of 3D Multi-material Parts Using Laser-based Powder Bed Fusion; In: 28th Proceedings of the Solid Freeform Fabrication Symposium 2017
[2] D. S. Weiss & M. Abkowitz, Organic Photoconductors, Bd. 93; In: Springer Handbook of Electronic and Photonic Materials, Kasap, Safa; Capper, Peter (Ed.). Cham.
Springer 2017
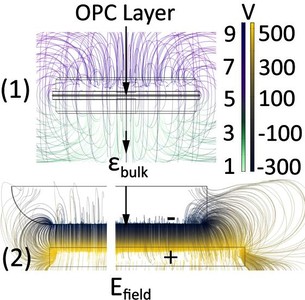