Finite Element Analysis Study of P-U Based Acoustic Vector Sensor for Underwater Application
An Acoustic Vector Sensor (AVS) is a compact device used for finding azimuthal as well as elevation angle of an acoustic source using particle velocity and pressure measured at the acoustic center of the device. There are mainly two types of AVS; namely P-P and P-U based AVS. P-P based AVS indirectly measures particle velocity and pressure using pressure gradient and pressure mean of two closely spaced hydrophones placed at some small distance apart, whereas P-U based AVS use inertial sensors and a hydrophone to measure particle velocity and pressure. In this work, we have studied P-U based AVS. The advantage of using P-U based AVS is that it provides higher directivity as compared to a single omnidirectional hydrophone. Also, the size of a P-U based AVS is more compact as compared to the hydrophone array for getting the same performance. There are numerous designs of P-U based AVS, We have followed the design in which an inertial sensor is encapsulated by a rigid sphere within a viscoelastic rubber and covered by a rigid protective casing. The rigid protective casing is used so that the AVS can withstand hydrostatic pressure. Viscoelastic rubber is used as a suspension system to suppress non-acoustical vibration, it passes only acoustical vibration. In this paper, we have studied using COMSOL® the effect of materials used for protective casing and also on its thickness on the signal received at the center of the AVS. Acoustic shell interaction environment in COMSOL® for studying this effect in the frequency domain is used. We have chosen polyurethane, aluminum, nylon and titanium materials for studying their effect on the received signal. We have found that polyurethane provides minimum attenuation as compared to other materials. The analysis method shall be presented in details.
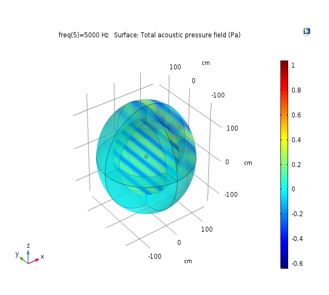
下载
- kumar_poster.pdf - 0.51MB
- kumar_paper.pdf - 0.38MB
- kumar_abstract.pdf - 0.07MB