Finite Element Simulation of Induction Heating of a Tubular Geometry
In Pressurised Heavy Water Reactors (PHWRs), the fuel bundles are located inside horizontal pressure tubes made of Zr 2.5 wt% Nb alloy. During reactor operation, pressure tubes undergo corrosion reaction with the heavy water coolant flowing through it and picks up a part of the hydrogen evolved. Assessment of the hydrogen concentration in the pressure tube forms part of the programme to assess the integrity of the component for continued operation. Presently, sliver samples are removed from the inside surface of the pressure tube and the hydrogen concentration is measured in laboratory from them using dedicated instruments. As the process involves considerable time and considerable radiation exposure, an insitu technique for the measurement is being developed. In this method, a tool head is inserted in the pressure tube and the hydrogen concentration is measured using an innovative technique. The tool head consists of a few modules and one of which is a split type induction coil for heating the pressure tube. Design of the coil geometry and other parameters are to be optimised to get the required heating pattern in the pressure tube. The flux from the induction coil also shall not interfere with the other modules which are a part of the tool head. The problem has been simulated using finite element software COMSOL Multiphysics. This paper gives details of the analysis carried out and the optimised parameters.
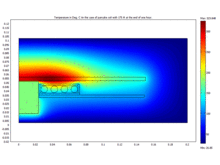
下载
- madhusoodanan_poster.pdf - 1.49MB
- madhusoodanan_paper.pdf - 0.82MB
- madhusoodanan_abstract.pdf - 0.16MB