Flow Calorimetry Modeling With Heat Transfer Module
We used COMSOL Multiphysics® simulation software to model mass flow calorimetry in a metal-hydride chemisorption reaction. Using a reaction chamber with 100W input, we measured the temperature of flowing water in contact with the chamber and calculated the heat output of our reaction. Experiments with non-reactive control samples found heat losses that can possibly be attributed to surface to ambient radiation, conduction, and convection. Using the Heat Transfer Module of COMSOL Multiphysics® (Heat Transfer in Solids and Fluids+ Laminar Flow), we modeled heat flux and used that information for insight on how to insulate our system and minimize the uncertainty incurred by external heat loss.
Our model geometry was a time-dependent 2D axisymmetric system with a multilayered reaction chamber, an inert solid and gas, a tube for gas pressurization, a resistive heater, and a water jacket, as shown in Figure 1. Assuming an inert sample and no external heat loss from the reaction chamber, we would expect 100W heat flux to be transferred by convective heat flux at the water jacket. However, experiments have shown that only 60W of energy is transferred by the water. We set the boundary conditions for the reaction chamber surface to convective heat flux, where the heat transfer coefficient h between flowing water and copper was roughly estimated from reference source [1]. Other boundaries were set to surface to ambient radiation, and the top of the tube had an outlet condition where gas could exit the system and convection could occur. To cross-reference our model with the experiment, we compared the temperature distribution of our COMSOL Multiphysics® model with our experimental temperatures and found that internal and water jacket temperatures were similar. We found that we could account for 85.51 by integrating with our given boundary conditions. Most of the heat loss came from conduction through the top of the reaction chamber into the top tube, with relatively minuscule amounts of energy lost through gas convection leaving the reaction chamber and through radiation from the exposed edge of the reaction chamber.
With our COMSOL Multiphysics® model in mind, we can potentially decrease conductive heat by adding insulating layers between our reaction chamber and top tube. Further measures can be taken to reduce the area of the top tube to reduce radiative loss in addition, although we suspect that those heat losses are minor compared to conduction.
References
[1] “Overall Heat Transfer Coefficients for Fluids - Heat Exchanger Surface Combinations.” [Online]. Available: https://www.engineeringtoolbox.com/overall-heat-transfer-coefficients-d_284.html. [Accessed: 11-Jul-2019].
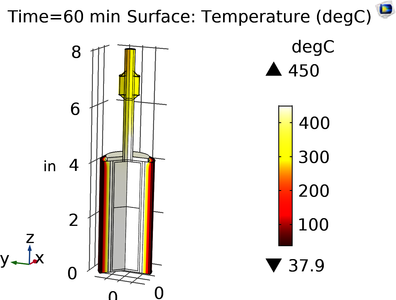
下载
- pham_poster.pdf - 1.21MB