Impact of Frictional Heat Generation upon Temperature of Sesame Paste Flow through Screw-expeller
Temperature of sesame paste flowing through a screw-expeller was studied. Screw-expeller used consisted of a rotating tapered screw and a constant-inner-diameter stationary barrel. Since screw diameter was much larger than the sesame paste thickness, an unwrapped model was employed with Cartesian coordinate x taken parallel to the barrel surface, y perpendicular to screw flights and z from screw root to barrel. Steady, fully developed, incompressible, creeping flow was assumed. Sesame paste was observed to exhibit shear thinning behaviour described by μ = K [(Ď:Ď)^(½)]^(n-1), where μ is viscosity, K is consistency coefficient, n is power-law index, [(Ď:Ď)^(½)] is shear rate and Ď is strain tensor expressed in terms of gradient of flow velocity (GŪ). Mass, momentum and energy balances available in the COMSOL Multiphysics® CFD Module were used. In the past literature, no-slip was assumed at paste/barrel and paste/screw interfaces and viscous heat generation, given by QV = 2μĎ:GŪ, was taken as the major heat source. In this study, slip at the paste/barrel interface and the resulting frictional heat generation (QF) were considered. QF is given as a surface integral of (pi) (λ p sf Db N), where λ is coefficient of friction at paste/barrel interface, p is pressure acting at paste/barrel interface, sf is slip factor at paste/barrel interface (sf=0 for no-slip condition and sf=1 for total slip), Db is inner-barrel diameter and N is screw rotational speed. Owing to the reduction in sesame paste thickness along x-direction, choice of mesh was crucial to the accuracy of the temperature field simulated and therefore a user-controlled mesh was used. Extra fine-sized free triangular mesh was created on the barrel surface boarded by extremely fine-sized mesh on either sides and they were swept down to the screw root surface through 20 fixed number of elements so that the reducing thickness of the sesame paste was adequately represented for numerical simulation. The choice of mess was guided by sensitivity analysis. Complete mesh consisted of 336880 domain elements, 98168 boundary elements and 6688 edge elements. Taguchi method was utilised to design the experimental study on the impact of sf, K and n upon the maximum temperature of flow. At sf=0, QF was zero and QV raised the flow temperature to a maximum of 0.7˚C above the inlet temperature. As sf was increased from 0 to 0.3, QF increased, almost linearly, to its highest at 13 W. Maximum temperature also increased, almost linearly, to its highest at 65.9˚C. As the temperatures recorded during the laboratory experiments (subjected to a maximum of 57˚C) were below 65.9˚C, investigations were not extended beyond sf=0.3. Simulation results showed that QF was more sensitive to sf than to K and n. This study, therefore, clearly demonstrated the importance of including slip at the boundaries and QF when modelling flow through screw-expeller.
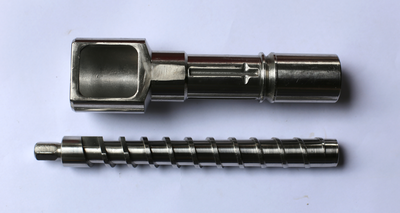
下载
- Europe_2020_Poster_Shanthini.pdf - 0.06MB
- Europe_2020_Paper_Shanthini.pdf - 0.34MB