MODELING MOISTURE DIFFUSION AND HYGROSCOPIC DEFORMATION IN EPOXY RESIN USING COMSOL MULTIPHYSICS
Rapid advancements in composites have positioned epoxy resins as a critical material in high-pressure applications such as water transport systems, oil and gas transport, and marine and aerospace applications. Epoxies are preferred over other materials due to their enhanced mechanical properties and resistance to severe environmental conditions (Placette et al., 2012). Despite these advantages, epoxy resin’s usability is limited due to its sensitivity to moisture diffusion, which often results in the degradation of its mechanical properties. This study aims to model the intricate dynamics of moisture diffusion within an epoxy resin subjected to extreme environmental conditions by adopting a numerical approach using COMSOL Multiphysics, thereby verifying experimental results.
Finite Element Analysis (FEA) was conducted to understand and simulate the complex diffusive behavior and hygroscopic deformation in epoxy resin, particularly in cyclic absorption-desorption cycles. Challenges included accurately predicting the dual-Fickian behavior in the initial absorption phase and its transition into Fickian nature for the subsequent cycles, along with correlating these results with observed mechanical deformations during the diffusive phases.
COMSOL Multiphysics 6.1 was utilized to simulate the coupled processes of water diffusion and mechanical deformations within the epoxy resin. Specifically, the Transport of Diluted species (tds) and Solid Mechanics (solid) modules were used to model water diffusion and resulting hygroscopic deformations, respectively. The robust multiphysics capabilities of COMSOL ensured a comprehensive understanding and analysis of the diffusion problem. Boundary conditions including initial and saturation concentrations, diffusion coefficients of dual-Fickian and Fickian curves, and hygroscopic coefficients, were extracted from experimental data. Models such as “Convection Cooking of Chicken Patties” and “MEMS Pressure Sensor Drift Due to Hygroscopic Swelling” from COMSOL’s application library were referenced to accurately set up the problem and validate the model.
FEA successfully validated the experimental findings, highlighting a dual-Fickian behavior in the initial absorption phase and a transition into Fickian nature in subsequent phases. The findings also emphasized the need for finer mesh refinements to accurately predict the non-Fickian nature of the initial absorption curve, whereas the process for subsequent phases is much more straightforward. The results for hygroscopic deformations closely matched experimental data. An almost linear relationship was found between specimen elongation and water content, although the hygroscopic swelling within the epoxy resin remains very low. A maximum elongation of 0.3% for 1.7% water absorption was found at the end of the first absorption phase. Interestingly, during desorption, the material recovered to its initial length even though the water content was non-zero.
This study highlights the efficacy of COMSOL in accurately modeling and predicting the diffusive behavior and hygroscopic deformation in epoxy resin. These insights can be used to enhance the material design of epoxy-based composites that are subjected to moisture-prone surroundings. Future research will focus on extending this model to composite structures while also studying the role of varying sample thickness on the diffusive behavior.
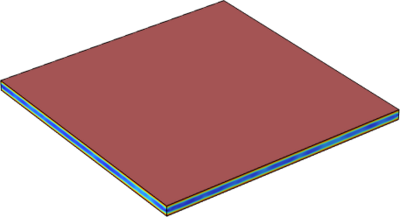
下载
- tarin_11061_poster.pdf - 0.9MB