Multiphysics Simulation of Battery Cells and Packs for Electric Vehicles
The scale up of electrical energy storage is one of the great technological challenges of our time as the world must quickly transform its energy infrastructure away from fossil fuels. Companies striving to commercialize new battery technologies must solve numerous electrochemical, thermal, and mechanical challenges in order to meet safety, cost, and performance targets. Multiphysics simulation of battery cells and packs can help meet these challenges and, in doing so, provide insights into battery performance and durability across numerous environmental and process conditions. We report here COMSOL Multiphysics® simulations of lifetime performance, thermal management, and structural durability of a lithium-ion prismatic battery pack for electric vehicle applications.
We simulated a hybrid pulse power characterization (HPPC) test of a fundamental prismatic cell across a variety of temperatures and states of charge using the Battery Design module (Figure 1). Without simulation, such a test would require days of experimental time. Figure 2 depicts a typical voltage response prediction during a charge-discharge cycle of the HPPC test, including voltage losses due to ohmic, activation, and concentration polarization. A key result from this study is the prediction of fast mass transfer in comparison to electrode kinetics, which is useful in determining the optimal loading of electroactive material in battery cells. Lastly, we calibrated a reduced-order model (ROM) of the single cell to efficiently run subsequent thermal simulations of battery packs with many cells. The ROM was developed using a Parameter Estimation study to calibrate parameters for a 0D Lumped Battery model.
We modeled liquid cooling in a prismatic battery pack using the Electrochemical Heating multiphysics coupling in conjunction with the Battery Pack and Heat Transfer in Solids and Fluids interfaces (Figure 3). During discharge, the battery pack dissipates power as heat. To manage temperature gradients in the pack, individual cells are separated by cold plates containing a network of parallel fluidic channels. Cool liquid injected on one side of the pack flows through the channels, where it absorbs heat generated by the batteries and then exits on the opposite side at a warmer temperature. Figure 4 shows that increasing the coolant flow rate increases the rate of heat absorption, thereby reducing the temperature gradients in the battery pack. A key result from this study is the prediction of liquid flow needed to maintain battery cells below a threshold temperature, which is important for the longevity and performance of the battery pack.
Finally, we predicted interfacial stresses in the battery pack using the Structural Mechanics module. Electric vehicle battery packs are subjected to mechanical loading during service that can cause cracks in adhesives to fail, eventually leading to a reduction in thermal control in the pack or ultimately to separation of the cell from the pack. Simulations such as these can be used to predict how changes in design would impact adhesive durability.
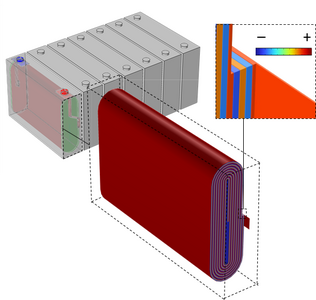