Numerical Simulation of Electronic Chip and Sink in a Horizontal Channel under Laminar Forced Convection
This paper investigates numerical simulation of electronic chips mounted on substrate of multilayer copper clad board (k = 40.5 W/m K) in a horizontal channel under laminar forced convection. The heat sinks made of aluminum ( k = 160 W/m K) is attached to the silicon chips in order to increase the heat transfer rate. Five silicon chips of size 15 x 15 x 5 mm are monted on substrate board of material single layer copper clad board. The rectangular fins of dimension 15 x 5 x 1 mm are attached to the base of size 15 x 25 x 2 mm. The fin base and fins are made of aluminum. The chips are subjected to uniform heat flux of 9500 W/m2. The heat transfer coefficient h = 5 W/m2 K is considered. This problem is modeled and simulated using COMSOL Multiphysics® commercial software. Heat Transfer Module was used to find heat transfer from solids, and conjugated heat transfer module is used to find full three dimensional heat transfer and fluid flow. The flowing air velocity of 2.5 m/s is used in laminar forced convection heat transfer. The results obtained are compared with other substrate board materials viz. silica/glass FR4, bakelite, and single layer copper clad board having thermal conductivities of 0.3, 1.4, and 8.8 W/m K. The results of temperatures show that the heat transfer using multilayer copper clad board is maximum. In general, it is found that the temperatures are decreasing with the increase in thermal conductivity of substrate board. Fig. 1 shows that the heat transfer from solids i.e. multilayer copper clad substrate board, silicon chips, and aluminum heat sinks.
The ambient temperature was considered to be 303.15 K (30°C). The maximum temperature obtained using multilayer copper clad board was found to be 347.9 (44.7°C) which is lowest among all substrate boards considered in this study. Hence the multilayer copper clad board is a better choice as substrate board for cooling of electronic components in electronic and IT industry. Fig. 2 shows the computer generated temperature contour plot. It indicates that temperature at the chips is increasing in the direction of flow. At the entry, it is lowest and increasing from silicon chip no. 1 to 5.
The direction of heat flow is shown by arrow volume in Fig.3. It is observed that heat is flowing in all directions as shown by the black arrows.
Keywords: Heat transfer from solids, heat flux, horizontal channel, electronic cooling.
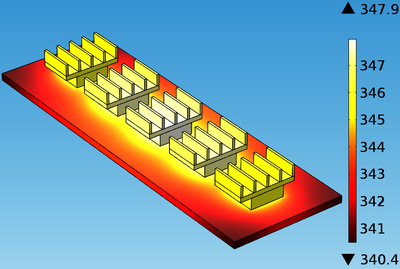