Numerical Simulation of the Laser Cutting Process for Dismantling
Laser cutting process is usually employed in machining process, however it is also applied for dismantling nuclear facilities. Contrary to mechanical processes where tools wear out quickly and are often renewed, laser cutting process is a contactless approach, therefore there is no deterioration caused by friction between tools and samples. Another advantage of this process is the ability to cut high-thickness with precision. Laser cutting uses the laser beam to melt the metal and the assisting gas ejects the melted metal (figure 1). The laser energy can be split in two part, on one hand the consumed part by the metal and on the other hand the incident part which doesn’t interact with the sample. This transmitted part (figure 1), called residual laser energy, is dangerous for structures in the background since this energy affects thermally and mechanically those structures (sealing problem and mechanical strength) and must be predicted of calculated.
The aim of this communication is to present both 2D and 3D models under development with COMSOL Multiphysics® answering to the residual laser energy by modelling the laser cutting process with heat and fluid flow equations in all states (gas, liquid and solid). A level set method is employed to capture the kerf dynamic evolution. Different meshes adapted to each physic and equation are used in order to reduce computation time without decreasing significantly the accuracy of the model. The methodology to calculate the laser propagation is currently under investigation.To validate the model, an experimental confrontation with high-speed camera observations is proposed to compare the kerf shapes, fluid velocities and flow behaviour according to the operating parameters.
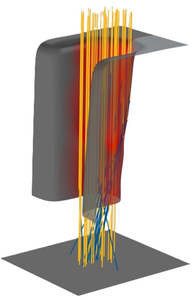
下载
- Meillour_5701_poster.pdf - 1.17MB