Simulation Driven Design of Blood Warmer
Blood Warmer is a movable instrument intended to deliver peripheral warmth to the arterial piping so as to keep the blood under warm conditions or liquid passing by throughout transfusion. The instrument is used to keep the blood or fluids under desired warm states before to transfusion to a subject. Blood warmers are frequently utilized in emergency units, normal medicinal rooms, and intensive care cells to avoid hypothermia. The instrument keeps the blood to a desired temperature that is nontoxic for infusion. American standard defines ASTM F2172 – 02 titled as “Specification for Blood/Intravenous Fluid/Irrigation Fluid Warmers”. The purpose of these specifications is to originate necessary quality conformance requirements for blood warmers devices. The standard actually decreases or eliminates risks of damages to subject and also the medical service provider and to stipulate testing by which fulfillment of requirements can be authenticated. Though current blood warmers can heat blood to the human body blood temperature, the challenges are temperature management, heat mapping across plate, optimum sensor location and the determination of the right compensation factor for dynamic control algorithm. During the concept design phase of the blood warmer, biomedical engineers at HCL had to review multiple heat transfer technology concepts like countercurrent heat exchanger, convective air, Magnetic induction, joule heating, microwave heating. COMSOL Multiphysics® was used at the concept phase to evaluate all types of physics. The tubular resistance heating technology which has a silicone heater patch and hollow aluminum tube through which the fluid tubing passes was selected based on the thermal efficiency results. The correlation between testing and COMSOL Multiphysics® simulation results was very good. The transient conjugate heat transfer simulations were coupled with MATLAB® for creating the algorithms, which was possible because of the virtual prototyping capability of COMSOL®. The product development process has been shortened in the concept and prototyping phase by effectively using COMSOL Multiphysics®. The heat transfer reports generated by using COMSOL® were submitted as supporting documents for regulatory purposes (FDA submission) and successfully got approvals to quickly move to mass manufacturing stage.
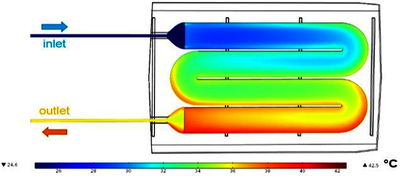
下载
- kapuganti_poster.pdf - 1.67MB
- kapuganti_paper.pdf - 0.33MB
- kapuganti_abstract.pdf - 0.01MB