Stress Analysis of Flexible Glass in a Large Deformation Test Setup
Ultra-thin flexible glass with thicknesses of 100 µm or below is bendable and has superior surface properties (Figure 1). The current use in foldable displays of mobile devices gives an idea of the range of possible applications [1]. However, it requires dedicated handling and processing due to its brittleness. Moreover, process chains must be adapted to allow pilot and industrial scale functionalization, e.g. vacuum coating of flexible glass. Therefore, data about the mechanical reliability is needed.
While several fracture strength testing methods have already been adapted to the special needs of flexible glass testing, fatigue testing has been mostly limited to static methods and has been performed comparatively rarely [2-3]. The most likely reasons for this are the long duration of fatigue tests and the random nature of glass strength. Due to the latter, minimum sample set sizes of 30 individual specimens are required to obtain reliable results. Despite these challenges, managing fatigue fracture – especially early-life fatigue – is crucial to reach viable production yields.
That’s why, a new method for dynamic fatigue testing has been developed. For this method, a U-Shape Folding tester by Bayflex Solutions (Figure 2) is used. The fatigue strength is estimated by conducting short fatigue tests but increasing the load stepwise. Thus, testing a sample set of 30 individual specimens takes no longer than 20 hours. The substrate deformation starts from the flat substrate (Figure 3): First, the substrate holders are simultaneously rotated and moved towards each other. The substrate is thereby deformed from a hor-izontal flat state into a drop shape. Secondly, the substrate nestles on a contact surface and is further deformed in a U-shape.
A nonlinear COMSOL® study using the Structural Mechanics Module is utilized to analyze the stress distribution during this complex deformation. For this purpose, a 3D-Model using shell elements was created and the penalty method was used for contact simulation. Parameters of interest are the maximum stress, the effective length of the loaded zone as well as the influence of the load rate on the maximum stress. The simulation results will be compared to the approximated maximum stresses determined using basic mechanical relationships of bending radius and resulting stress. By the means of the simulation results the (fatigue) strength of coated glass can be analyzed more precisely. This should facilitate estimations of suitable handling parameters during processing.
The author gratefully acknowledges the COMSOL Support for substantial assistance with model creation especially regarding the nonlinear contact analysis.
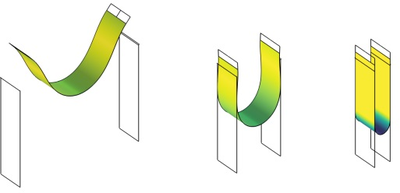
下载
- Langgemach_5951_presentation.pdf - 3.53MB