Thermal Management of High Power Electronics using COMSOL Multiphysics® Simulation Software
Increased demand for high power electronics has required increasingly more efficient thermal management techniques. Simple cold plates using tubes or channels are frequently used to cool high power components but restrictions on size, weight, and power have restricted their effectiveness. This project analyzed several thermal management approaches using additive manufacturing to dramatically increase performance with novel materials and structures that could not be fabricated using traditional methods.
Conventional cooling methods flow coolant parallel to the heat source surface in a serpentine path under components. In parallel flow, a thermal gradient develops across the channel which diminishes the heat transfer effectiveness across the channel width. In addition, the coolant temperature increases as it removes heat from each component, becoming less effective as it progresses.
Using multiphysics simulation software, a cold plate design using manifolds and microchannels was designed to maximize cooling efficiency by dividing the coolant into several parallel paths and directing the flow into microchannels at a direction coolant perpendicular to the heated surface. After a short length through the microchannels, the coolant returns to an adjacent manifold and exits the plate. By increasing the surface area and minimizing the microchannel path length, very large heat transfer coefficients are obtained with a corresponding low cold plate thermal resistance.
Using COMSOL Multiphysics® simulation software for heat transfer and laminar flow, the microchannel spacing, coolant flow rate, and manifold sizing have been determined to maximize heat removal and minimize pressure drop. Thin cold plates (<4 mm thick) were designed, and using direct metal laser sintering, aluminum, copper, and titanium cold plates were printed, tested, and compared against COMSOL simulation results.
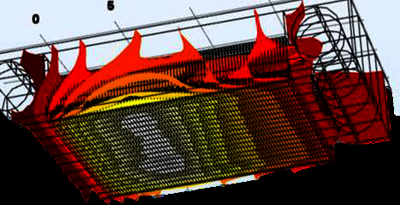
下载
- bratt_heatrans_presentation.pdf - 2.51MB