Towards Automatic Defect Recognition using Active Infrared Thermography, COMSOL Multiphysics® and Machine Learning
Active Infrared Thermography (IRT) is a family of non-destructive testing (NDT) techniques used for the detection of surface and buried defects in a wide range of materials. The method is robust and sensitive enough to be used even in harsh industrial environments
However, the automatic detection and sizing of real defects using IRT can still be challenging, as the fabrication of physical calibration blocks with artificial defects that correctly represent the large variety of real defects is expensive and can be difficult, if not impossible, for many cases.
To solve this particular challenge, COMSOL Multiphysics® has been used to create a range of models for different types and geometries of defects, and to create computationally the experimental conditions used in IRT by modeling the thermal behavior of virtual calibration blocks. Moreover, with very little effort, the models could be adapted for different materials and sizes.
Finally, Machine learning algorithms, such as non-supervised or supervised models such as k-means clustering or artificial neural networks (ANN), have been used to automatically detect, position and size defects and defect clusters in 3-dimensions.
This paper presents the use of these techniques to predict the position of computationally created flat bottom holes (FBH) defects and to compare the results against the same defects in a physical calibration block. The model uses the COMSOL Multiphysics® Heat Transfer module to create a model of an FBH defect illuminated by a Flash lamp source and parameterize it for different FBH diameters and top layer thicknesses (see (a)). In addition, a complete simulation of an artificial calibration block of 42 FBHs was created (see (b)) for direct comparison with the IRT thermal experiments (see (c)).
K-means clustering methods can be used on post-processed data for defect-recognition in a non-supervised manner (see (d)). Furthermore, ANNs can be further trained to recognize and size any type of defect.
In conclusion, it could be shown that these combined procedures can create extensive training sets for automatic defect recognition and sizing via Machine Learning for any type of defect, reducing or eliminating the need for physical models.
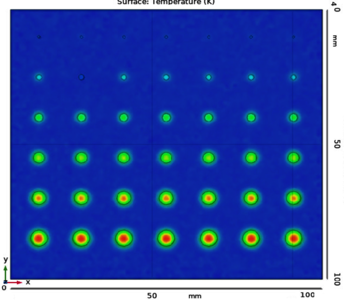
下载
- Cambridge_2019_Poster_PT.pptx - 1.55MB