Two-Phase Flow Modeling of Metal Vaporisation under Static Laser Shot Using a Double ALE Method
Additive manufacturing gathers technologies where near net shape components are produced by depositing successive layers of materials. Among these technologies, the Layer Beam Melting (LBM) process – often referred to as Selective Laser Melting (SLM) – is garnering industrial interest, especially in the aerospace field. It allows shape flexibility and hence brings the opportunity to rethink and optimise the components and their functionalities.
Based on the interaction between a laser source and a metallic powder bed, LBM is associated with complex physical phenomena: powder energy absorption and melting, convection within the melt pool, matter vaporisation, and so on [1]. Particularly, alloy vaporisation induces collateral effect as powder bed denudation or ejection of melt and nano/micro particles [1]. These latter may either interact with the laser source – and thus reduce the melt pool energy absorption – or contaminate the powder bed, creating inclusions. It is therefore necessary to understand these physical phenomena to control the process, reducing instabilities and limiting the appearance of defects as porosities and cracks.
In this prospect, a two-phase flow model of metal vaporisation under laser irradiation is proposed. In this feasibility study, the powder layer is first omitted and computation is performed on a 2D axisymmetric geometry to save numerical resources. In both domains, heat transfer and fluid flow equations are fully coupled and the liquid/gas interface is tracked using the Arbitrary Lagrangian Eulerian (ALE) method. Relevant interface jump conditions are thus manually included to couple the two separated domains. Laser drilling and welding have previously been subjected to numerical study using ALE, but the analyses were restrained to the metal phase [2,3]. Hence, the proposed approach is unprecedented.
In the metal phase, the solid/liquid interface is modelled using a Darcy’s law and at the liquid/gas interface, surface tension and thermocapillary convection (Marangoni effects) are included. The recoil pressure induced by metal vaporisation – driven by the liquid/gas interface temperature – is also taken into account, based on an improved analytical expression. In the gas phase, the metal vapour plume and the induced compressible gas flow are computed. Furthermore a second calculation step which integrates gas/particles interactions is added with the aim to validate the plume velocity thanks to the particle tracing module.
The present model will be performed in 3D in future works with representative SLM conditions. It should be able to link the process parameters to the bead shape and dimensions – as numerical model from the literature usually do – and more importantly to the induced gas flow in the building chamber. This new contribution will be the base of a study of the interaction between the metal vapour plume and the gas circulation system of the LBM machine.
[1] V. Gunenthiram, P. Peyre, M. Schneider, M. Dal, F. Coste, R. Fabbro, J. Laser Appl. 29 (2017) 022303. [2] V. Bruyere, C. Touvrey, P. Namy, in: Proc. 2013 COMSOL Conf., 2013, pp. 1–7. [3] I. Tomashchuk, I. Bendaoud, P. Sallamand, E. Cicala, S. Lafaye, M. Almuneau, in: Proc. 2016 COMSOL Conf., 2016, pp. 1–7.
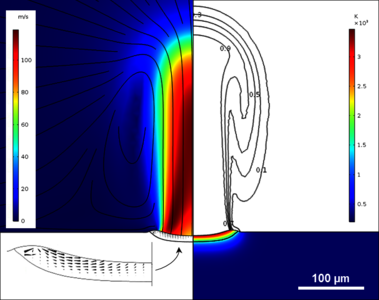
下载
- mayi_presentation.pdf - 1.16MB
- mayi_poster.pdf - 2.66MB
- mayi_paper.pdf - 0.86MB
- mayi_abstract.pdf - 0.07MB