Modeling and Simulation of Damping Resistance of a Cantilever Based Energy Harvester
The multilayer composite single mass cantilever is a MEMS energy harvester structure. The vibrating structure is under vacuum in hermetic MEMS. However, out-gassing during process integration and fabrication would cause air molecules (e.g. hydrogen, nitrogen, argon, water vapor, oxygen, ammonia, nitrous oxide, carbon dioxide, carbon monoxide, etc.) to be present in the cavity, and therefore vary the cavity pressure.
The present study is aimed to predict the damping (measured as Q-factor) of a single mass cantilever energy harvester structure (as shown in Figure 1) at various cavity pressure using COMSOL Multiphysics® commercial finite element software. Lower Q-factor due to lack of vacuum leads to loss of the harvested energy, and makes the device practically useless for most applications. Varying the pressure from atmospheric to near vacuum conditions, we calculate the Q-factor of the structure due to squeeze film, slide film, and thermo-elastic damping. The anchor loss (another source of damping in MEMS structure) has been neglected in the present study. Our results show that at near vacuum pressure, the air damping (squeeze and slide film) is negligible and, rather, the intrinsic damping of the structure (thermo-elastic damping) predominates. In the transitional region – transition between viscous and molecular flow—squeeze film damping becomes the predominant mechanism and the Q-factor demonstrates a linear response to pressure in the log-log scale.
This trend has been verified by experimental data for other MEMS structures. The micro-scale thickness of the cantilever implied a negligible slide film damping between the cantilever arm and the cavity sidewall. In the viscous regime – pressures close to atmospheric conditions—the Q-factor shows a minimal response to pressure. These observations are in good agreement with the theoretical response of an oscillating cantilever in the viscous, transitional and molecular regimes [1]. Furthermore, COMSOL results have been compared with a validated model and it shows a good agreement (as seen in Figure 2). Attempts were made to model the cantilever oscillation using a coupled Fluid-Structural-Interaction (FSI) model.
However, issues related to excessive computational time and numerical damping were experienced. We present a technique to minimize the FSI model’s computational time by developing a frequency domain fluid mechanics solver and alleviate numerical damping by adapting adequate solvers and tolerances.
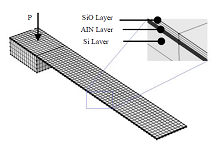
下载
- ali_presentation.pdf - 2.02MB
- ali_paper.pdf - 0.61MB
- ali_abstract.pdf - 0.13MB