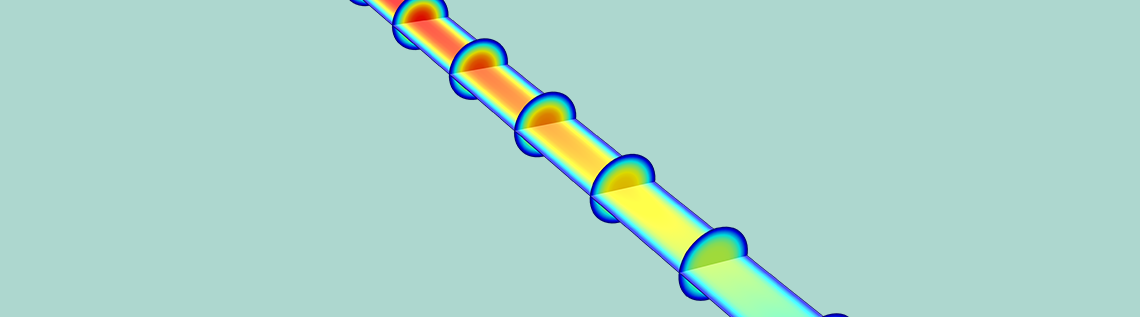
管式反应器是化工行业中经常使用的一种设备,帮助进行连续大规模的生产。通过模拟管式反应器的解离过程,可以对这些设备进行准确分析。在这篇文章中,我们通过对等温和非等温模拟研究的比较,展示了 COMSOL 化学反应工程模块的许多有用功能。您也可以在自己的仿真中使用这些功能。
管式反应器:化学工业中的一种常见设备
如果你观察过管式反应器的内部,就会发现反应物在高速流动并不断进行反应。这些反应物在管道内移动的过程中被转化为产品。由于生产过程是连续的,这些设备通常可以有效地帮助化学和石油工业进行规模生产。
此外,管式反应器还被用在其他领域应用中,如发电厂和发动机的焚烧工艺中的废气处理。这种类型的反应器甚至可以用作药物的提纯,生产出价格更低的药品。
一个管式反应器模型
管式反应器是化工行业中经常使用的一种设备,用于帮助进行连续大规模的生产。通过模拟管式反应器的解离过程,可以对这些设备进行准确分析。在这篇文章中,我们通过对反应器等温和非等温情况下的模拟研究的比较,展示了 COMSOL 化学反应工程模块的许多有用功能。您也可以在自己的仿真中使用这些功能。
模拟解离过程
我们从一个旋转对称的模型开始对管式反应器进行分析。由于反应器的形状规则,因此模型使用了一个映射或结构化的网格。模型中使用了层流 和浓物质传递 接口,并设置了相关边界条件。
使用这个模型我们能够重点研究气相解离过程。在这个过程中,A 物质发生反应并形成产物 B。每 1 摩尔 A 反应后会产生 2 摩尔 B,使混合气体的体积发生膨胀。由于密度的变化,当混合物在反应器中移动时,气体的速度会增加,这种情况我们可以用可压缩的纳维-斯托克斯方程来模拟。
图示显示了管式反应器中的解离过程。
在解离反应中,混合物的成分发生了变化。一开始在入口处是纯 A,但在出口处变为 A 和 B 的混合物,成为一个多组分系统。当处理像这样一个浓的多组分混合物时,需要考虑到所有可能的相互作用。在这个案例中,我们使用了浓物质传递 接口和 Maxwell-Stefan 或混合平均扩散方程来描述所有这些成分之间的相互作用。
此外,根据理想气体定律,密度的变化取决于压力、温度和成分。在浓物质传递 接口中,关于密度的 “理想气体 “选项将自动考虑所有这些因素。层流 接口描述了考虑密度变化的流体的动量平衡和连续性。
在模型中,B 的生产速度取决于成分和温度。然而,如果假设气体是等温的,那么该速率将只随成分变化。我们将通过比较等温研究和非等温研究(同时考虑成分和温度)来看看这对结果有什么影响。
比较等温和非等温研究
管式反应器的等温研究求解了可压缩的 Navier-Stokes 方程和 Maxwell-Stefan 对流和传导方程的耦合模型。该模型会在非等温情况下进行扩展,为此我们将增加流体传热 接口和能量平衡方程来模拟温度变化的影响。
在等温情况下温度保持在 473K 不变,而在非等温情况下温度会发生变化。对于后者,气体在 293K(室温)的温度下进入反应器,反应器壁则被加热到 473K,所以在反应过程中,温度会逐渐升高。因此,这两个模型之间的一个主要区别在于它们如何处理温度。
这种温度上的差异会影响到研究的其他方面。例如,我们仔细看一下速度的大小。当对以上两种情形进行比较时,可以看到,由于反应过程中混合气体的体积扩大,速度沿Z轴增加。然而,在非等温情况下,速度略小。这是因为非等温情况下的温度较低,因此反应速率也较低。
比较等温(左)和非等温情况(右)下的速度大小。可以看到,在等温情况下,最大速度要大一些。
我们还对两项研究中物质 B 的质量分数进行了比较。比较下面两副图可以发现,对于等温模型,在管子表面附近的物质 B 的质量分数比中心区域要高。这是由于靠近侧表面的对流速度较低。对于非等温模型,在靠近侧表面的区域质量分数也较高,但总体而言,质量分数低于等温情况。在观察出口处的物质 B 的平均质量分数时,这种差异很明显,等温情况下是 64.1%,非等温情况下是 26.4%。
比较等温情况(左)和非等温情况(右)下物质 B 的质量分数。
在等温研究中,出口处的平均转化率为 64.4%,非等温研究中为 24.2%。这进一步显示了温度对管式反应器性能的影响。从这些研究中,我们可以看到,温度曲线对反应器的反应和转化率有很大影响。
该模型可用于分析处于设计阶段的管式反应器,以及已经用于生产应用中的反应器的反应速率。您也可以在自己的模拟中应用这篇文章中提到的许多建模技术,包括考虑多组分扩散和用映射网格离散细长几何体。
了解更多关于化学反应工程和管式反应器的信息
- 自己动手尝试: 下载管式反应器中的解离反应教程模型。
- 阅读这篇博客,了解管状反应器仿真 App 如何用于数学建模教学。
- 查看管式反应器教程模型:
评论 (0)