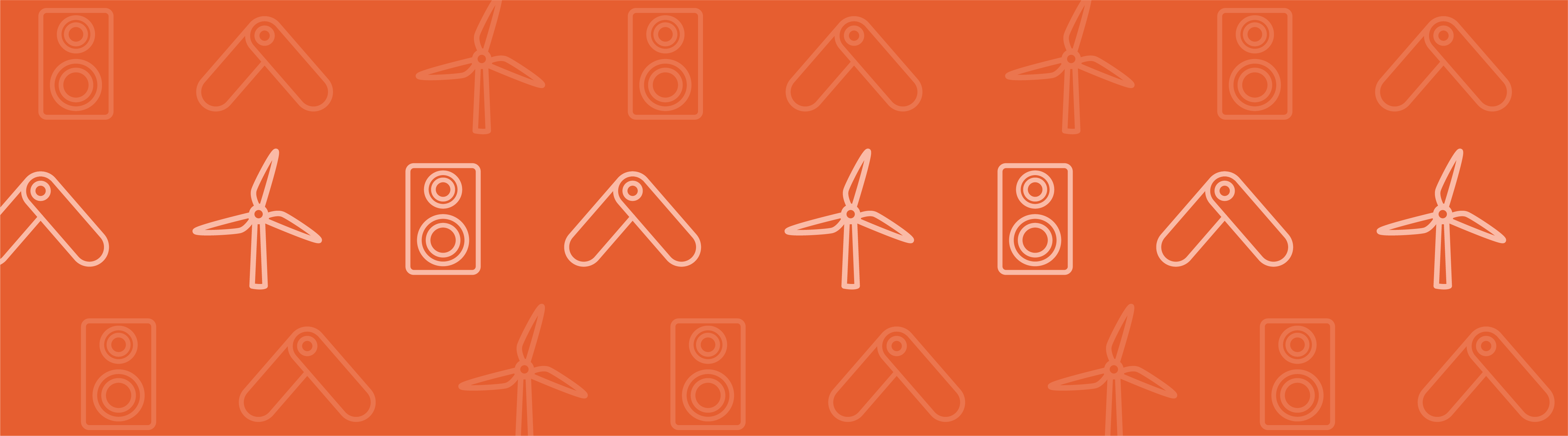
卡车吊机常用于处理各种载荷,经常需要搬运沉重的材料,它们会给吊机的各个不同零件带来较大的力。看看仿真如何帮助确定这些力带来的影响,以及如何改进吊机的操作。
一台会移动的机器
吊机被设计用来提供一种机械优势,它可以提起或放下单靠人力无法处理的沉重材料。在吊机的诸多应用场景中,从建筑到电线维护,它的移动性都是一个相当突出的特征。卡车吊机可以向不同方向移动,还可以在高速公路上行驶,免去了对运输设备的需求。
卡车吊机示例。(“由澳大利亚普尔芬格 (Palfinger) 制造的卡车吊机。混凝土组件是由德国制造的小型污水处理厂,最多可为一个生活有四位居民的小型住宅提供服务。”图片为 TM 自行拍摄。图片已获 Creative Commons Attribution-Share Alike 2.0 Germany 授权,且通过 Wikimedia Commons 分享。)
这类吊机包含几种用于控制吊机运动及其他机制的液压缸。当处理较重的载荷时,这些零件将承受较大的力。我们通过仿真探索了这些力在机械运行周期产生的影响,并通过开发一个更高效的设计确定了如何改进其性能。
对卡车吊机刚体的分析
耦合多体动力学模块和结构力学模块,卡车吊机模型分析了吊机的液压缸和铰链在一个操作周期中将承受的力。从 CAD 模型中导入吊机几何,其中包含 14 个会发生相对运动的零件。
卡车吊机几何。
下图是对吊机连杆的详细描述,之后的表格中定义了具体零件。
零件 | 颜色 |
---|---|
底座 | 蓝色 |
内悬臂 | 绿色 |
外悬臂 | 黄色 |
伸缩式延伸件 | 青色、紫红色、灰色 |
悬臂升降缸 | 红色、灰色 |
悬臂升降活塞 | 黄色、紫红色 |
内部连杆 | 紫红色、黑色 |
外部连杆 | 青色、蓝色 |
本示例中包含两个载荷:负 z 方向的自重,以及吊机端点的有效载荷。操作周期包含从很远处举起一个有效载荷,然后将其置于吊机下方。载荷最初经过向上的移动,然后向内移动到靠近吊机处。下图显示了吊机端点在操作周期中的轨迹。
吊机端点在操作周期的轨迹。
在现实中,吊机的操作由三个液压缸的长度确定,即内液压缸、外液压缸,以及伸缩式液压缸。内液压缸将举起内悬臂,外液压缸调节内悬臂与外悬臂之间的夹角,伸缩式液压缸则确定了伸缩范围。这里将使用悬臂夹角而非液压缸长度作为参数,因为这样更加方便。
结果
下图显示了操作周期的第 9 个位置,此时内悬臂呈水平 45°角,内悬臂与外悬臂夹角为 -30°,总伸缩为 1.5 m。
位于操作周期第 9 个位置的吊机;颜色显示了吊机零件的总位移。
我们现在可以分析力对吊机不同零件的影响。在之下的每张绘图中,解的序号都与吊机位置相关。最初,吊机会在延伸位置抓起一个载荷,最后在靠近本身处释放载荷作为结束。
让我们先从控制悬臂的液压缸上的力开始,此处的压缩力为正。正如我们所预期的,当有效载荷远离吊机底座时,液压缸受到较大的力。操作周期中的最大力确定了所需的液压缸容量。
控制悬臂的液压缸上的力。
下一张绘图突出了伸缩式液压缸中的力。与前面的情况相同,压缩力定义为正值。由于内液压缸需要将伸缩部分的重量搬运到更远的距离,因此要承受更大的力。
伸缩式液压缸中的力。
最后,我们可以观察到作用在吊机主要零件之间的铰链上的力。可使用相同策略来分析作用在吊机任意两个零件间的连接部位受到的力。下图结果就是一个包含此类细节的结构尺度上的有价值信息。
铰链上的力。
锁定系统中的一个具体机制
现在,我们可以再进一步,使用优化模块来增强吊机的连杆。这可以通过优化吊机连杆模型实现,这是卡车吊机模型的一个扩展模型,重点关注当吊机在最坏负载循环情况下拖拽特定载荷时,如何降低液压缸上的力。
连杆的细节图。
下表确定了每个零件及它们在模型中的表示颜色。
零件 | 颜色 |
---|---|
底座 | 蓝色 |
内悬臂 | 绿色 |
悬臂升降缸 | 红色 |
悬臂升降活塞 | 黄色 |
连杆 | 紫红色、黑色 |
由于本示例被设计用来测试最坏的情况,所以在选定的操作周期中,连杆将承受最大的力。为确保这一点,内悬臂将被提升至最高位置,伸缩式延伸件被拉伸至最远状态,并选定了外悬臂的角度以保证吊机端点尽可能地向外伸展。所施加的载荷与原始模型中相同。
在此优化问题中,可以修改三个轴的位置:连接第一连杆臂与底座的轴、连接第二连杆臂与悬臂的轴,以及连接两个连杆臂与液压缸活塞的轴。
对比设计
现在让我们对比一下结果。下方的第一张绘图显示了液压缸上的力在操作周期中的变化。这里,我们可以对比操作周期中用来确定液压缸容量的最大液压缸力。
与原始设计相比,优化版本将最大力从 597 kN 降低到了 413 kN, 即降低了 31%,这是一个相当大的进步。优化后,将能支持更重的有效载荷;作用力的降低,使连杆可以更轻松地面对应力极限。
对比优化和原始设计中液压缸上的力。
第二张绘图显示了 y 和 z 分量,以及作用在轴上的力的大小,这些轴形成了底座和悬臂之间的铰链。如下方结果所示,原始设计中的总力大于优化设计中的总力。
优化和原始设计中轴上的作用力。
总结及模型下载
在 COMSOL Multiphysics 5.0 版本中,我们引入了两个新的卡车吊机模型,可用于分析吊机不同零件间的相互作用,以及评估优化方法在增强这些机制方面扮演的角色。这些示例演示了您可以如何使用仿真来分析载荷对这些复杂力学系统的影响,以及如何根据仿真结果来开发一个更优的设计。
下载文中介绍的模型:
最后再说一下,我们正基于此模型创建相关 App,请继续保持关注!
评论 (0)