显示活动时间: 00:00 – 00:00
搜索
近期活动
正在加载活动内容
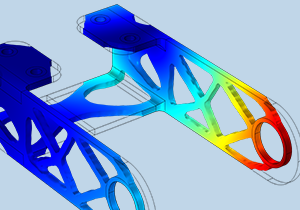
2024 年 12 月 26 日
| 01:00 HKT
使用 COMSOL Multiphysics® 优化设计
COMSOL
网络研讨会
线上
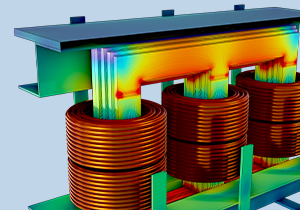
2025 年 1 月 2 日
| 21:00 HKT
COMSOL® 中的低频电磁场仿真
COMSOL
网络研讨会
线上
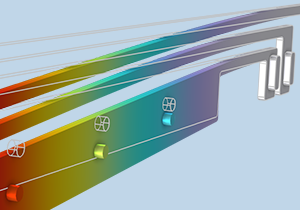
2025 年 1 月 8 日
| 01:00 HKT
COMSOL 多物理场仿真简介(在线演示)
COMSOL
网络研讨会
线上

2025 年 1 月 15 日
| 00:30 HKT
COMSOL 主题日:6.3 版本
COMSOL
COMSOL 主题日
线上
显示活动 4 场,活动总数 4 场。
Date | Time | Title | Type | Host | Discipline |
---|---|---|---|---|---|
2024 年 12 月 26 日 | 01:00 |
使用 COMSOL Multiphysics® 优化设计 |
网络研讨会 | COMSOL-线上 |
|
2025 年 1 月 2 日 | 21:00 |
COMSOL® 中的低频电磁场仿真 |
网络研讨会 | COMSOL-线上 |
|
2025 年 1 月 8 日 | 01:00 |
COMSOL 多物理场仿真简介(在线演示) |
网络研讨会 | COMSOL-线上 |
|
2025 年 1 月 15 日 | 00:30 |
COMSOL 主题日:6.3 版本 |
COMSOL 主题日 | COMSOL-线上 |
|
视频培训中心
网络研讨会视频点播
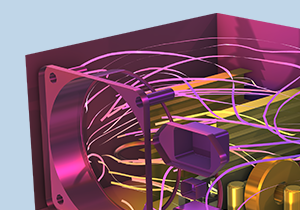
COMSOL® 中的传热仿真
网络研讨会
Dec 12
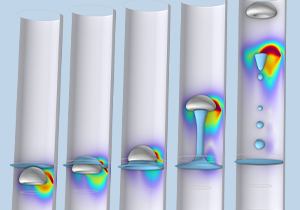
COMSOL® 中的多相流仿真
网络研讨会
Dec 05

COMSOL Multiphysics® 6.3 版本功能简介
网络研讨会
Nov 28
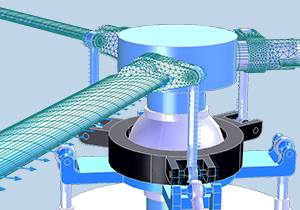
COMSOL® 中的转子动力学和多体动力学仿真
网络研讨会
Nov 21

COMSOL® 求解器介绍及设置方法
网络研讨会
Nov 14
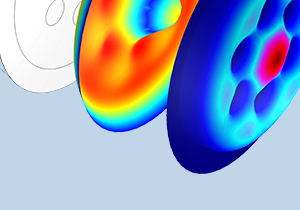
使用 COMSOL Multiphysics® 模拟声学超材料
网络研讨会
Nov 07
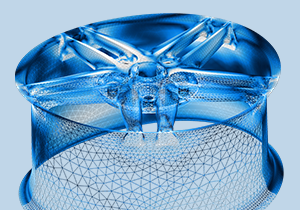
多物理场仿真结果的处理与可视化
网络研讨会
Oct 24
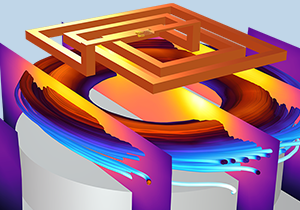
COMSOL® 中的等离子体仿真
网络研讨会
Oct 17
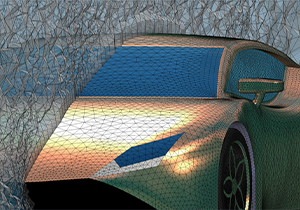
COMSOL® 网格划分功能介绍
网络研讨会
Oct 10
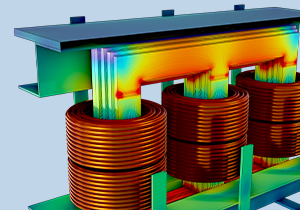
电力变压器的多物理场仿真
网络研讨会
Sep 19
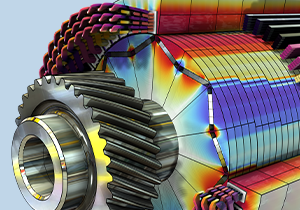
使用 COMSOL Multiphysics® 仿真高性能电机
网络研讨会
Sep 12
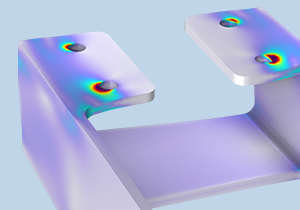
不确定性量化在多物理场仿真中的应用
网络研讨会
Sep 05
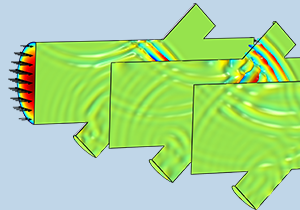
超声波及其应用的多物理场仿真
网络研讨会
Aug 29
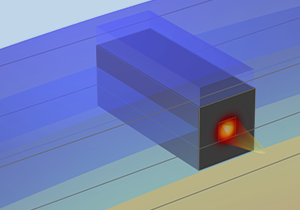
使用 COMSOL Multiphysics® 模拟光电半导体
网络研讨会
Aug 15
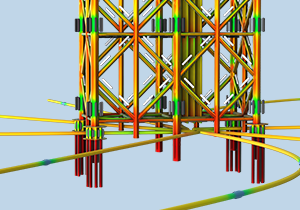
COMSOL® 多物理场仿真加速数字岩心技术发展
网络研讨会
Aug 08
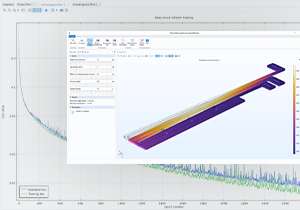
使用代理模型开发高效的 COMSOL® 仿真 App
网络研讨会
Aug 01
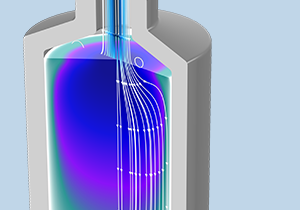
COMSOL® 多物理场仿真在地热能开发中的应用
网络研讨会
Jul 25
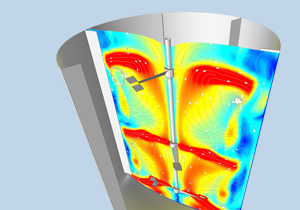
COMSOL® 仿真 App 开发、部署和应用
网络研讨会
Jul 18
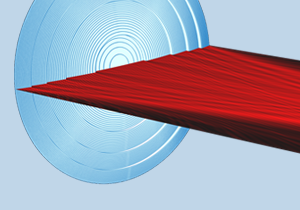
COMSOL® 中的光学仿真
网络研讨会
Jul 11
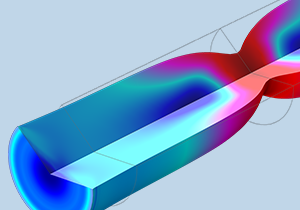
非线性结构材料参数估计
网络研讨会
Jul 04
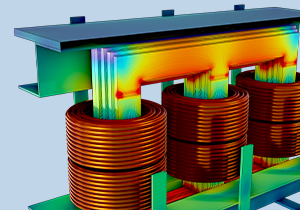
基于 COMSOL® 构建电力设备的数字孪生
网络研讨会
Jun 27
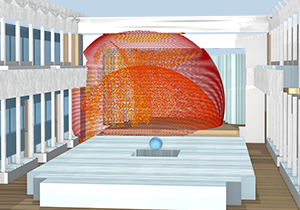
COMSOL® 室内声学仿真
网络研讨会
Jun 20
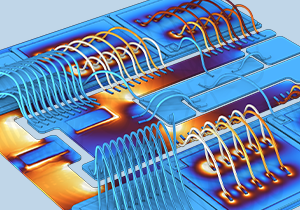
COMSOL Multiphysics® 在半导体制造中的应用
网络研讨会
Jun 13
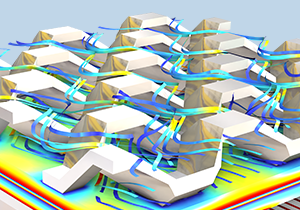
COMSOL Multiphysics® 在绿氢技术中的应用
网络研讨会
Jun 06
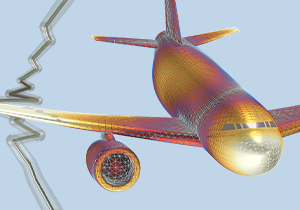
使用 COMSOL Multiphysics® 模拟放电现象
网络研讨会
May 28
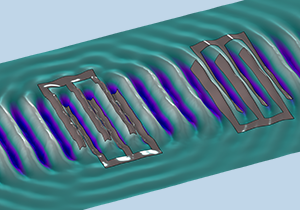
使用 COMSOL® 模拟 SAW/BAW 器件
网络研讨会
May 16
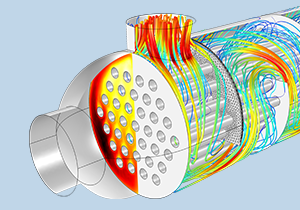
COMSOL® 中的换热器仿真
网络研讨会
May 09
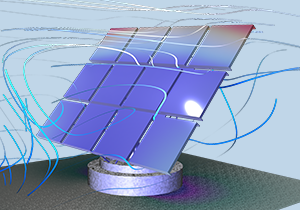
COMSOL Multiphysics® 中的流固耦合仿真
网络研讨会
Apr 18
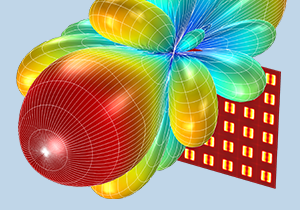
多尺度电磁波仿真
网络研讨会
Apr 11
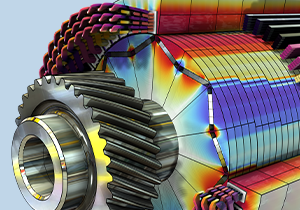
COMSOL® 微执行器和微型电机仿真
网络研讨会
Apr 02
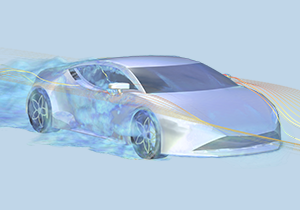
COMSOL® 中的湍流仿真
网络研讨会
Mar 26
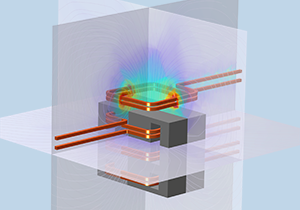
COMSOL® 仿真在电力电子技术中的应用
网络研讨会
Mar 14
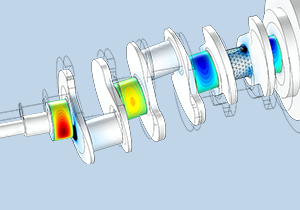
COMSOL® 中的流体动压轴承仿真
网络研讨会
Mar 12
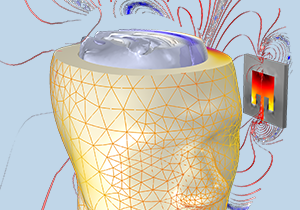
使用 COMSOL Multiphysics® 模拟 EMI/EMC 现象
网络研讨会
Mar 07
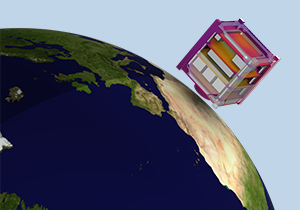
COMSOL® 中的热辐射仿真
网络研讨会
Mar 05
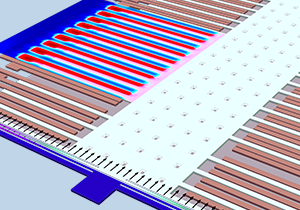
使用 COMSOL Multiphysics® 模拟 MEMS 加速度计和陀螺仪
网络研讨会
Feb 29
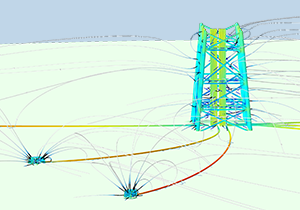
在 COMSOL Multiphysics® 中模拟腐蚀及防护系统
网络研讨会
Jan 25
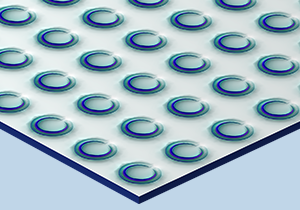
使用 COMSOL® 模拟等离激元效应和超材料
网络研讨会
Jan 18
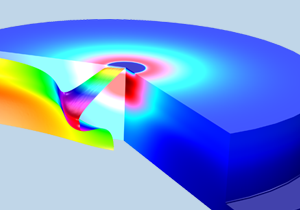
半导体封装和测试中的多物理场仿真
网络研讨会
Jan 11
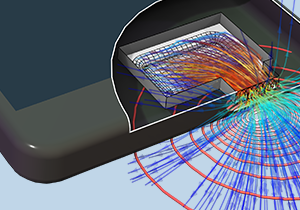
COMSOL® 中的扬声器和麦克风仿真
网络研讨会
Jan 04
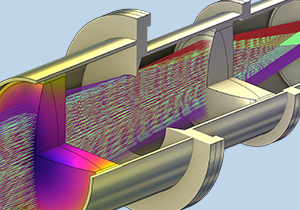
使用 COMSOL Multiphysics® 进行结构-热-光学耦合分析
网络研讨会
Dec 21
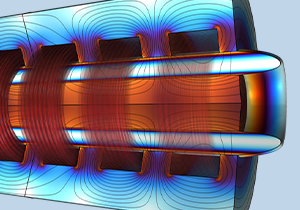
COMSOL® 多物理场仿真在电气绝缘中的应用
网络研讨会
Dec 05
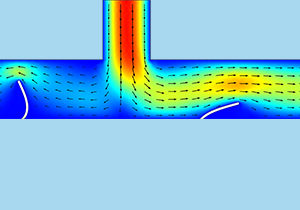
微流体器件的多物理场仿真
网络研讨会
Nov 30
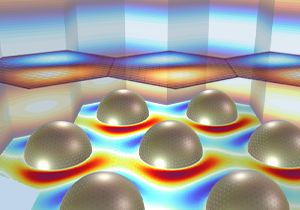
半导体制造中的晶体生长仿真
网络研讨会
Nov 28
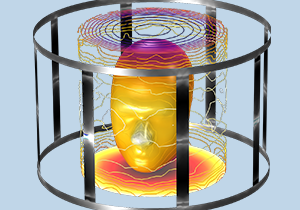
COMSOL® 多物理场仿真在医疗设备研发中的应用
网络研讨会
Nov 21
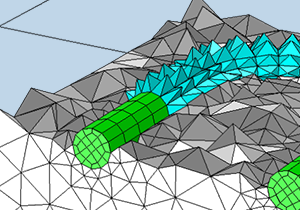
COMSOL® 中的网格划分
网络研讨会
Nov 16
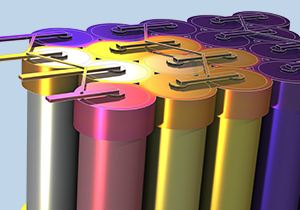
锂离子电池热失控仿真
网络研讨会
Nov 14
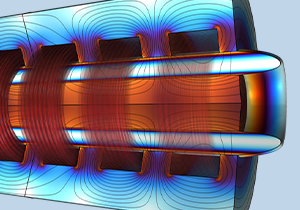
COMSOL® 中的磁流体仿真
网络研讨会
Nov 09
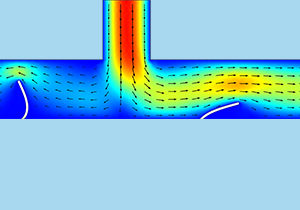
COMSOL® 地下水流及多孔介质流仿真
网络研讨会
Nov 02
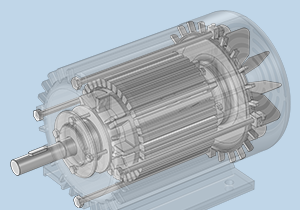
电磁噪声的仿真分析
网络研讨会
Oct 31
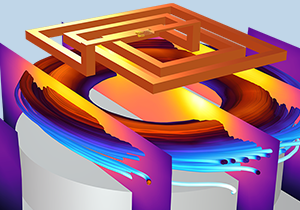
使用 COMSOL Multiphysics® 仿真 PVD/CVD 薄膜沉积工艺
网络研讨会
Oct 27
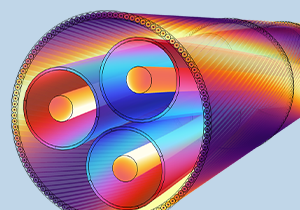
COMSOL® 多物理场仿真优化电缆设计
网络研讨会
Oct 20
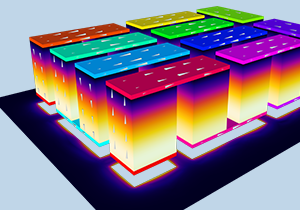
COMSOL® 的求解器简介
网络研讨会
Oct 13
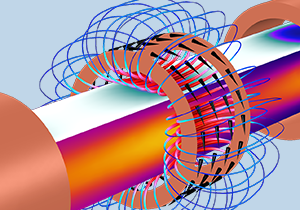
COMSOL® 中的感应加热仿真
网络研讨会
Sep 26
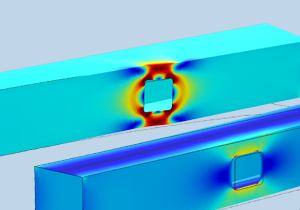
COMSOL® 中的岩土力学仿真
网络研讨会
Sep 19
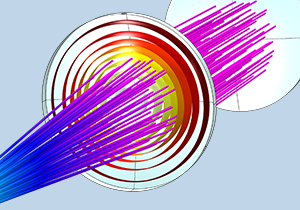
多物理场仿真在激光加工中的应用
网络研讨会
Sep 15
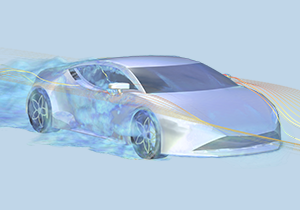
计算流体力学(CFD)多物理场仿真
网络研讨会
Sep 12
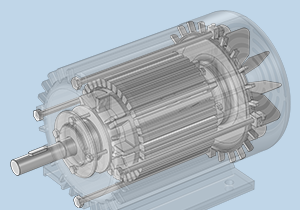
使用 COMSOL® 求解大型模型
网络研讨会
Sep 08
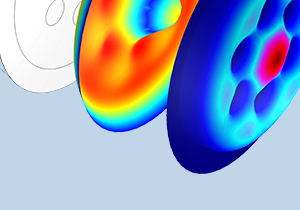
COMSOL® 中的声学超材料仿真
网络研讨会
Sep 05
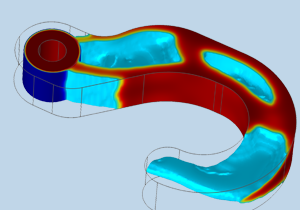
使用 COMSOL Multiphysics® 进行设计优化
网络研讨会
Sep 01
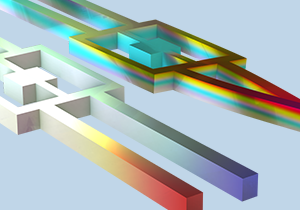
COMSOL® 的压电材料和器件仿真
网络研讨会
Aug 29
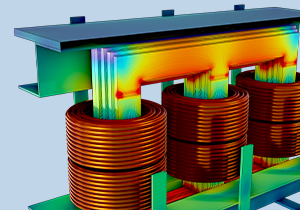
COMSOL® 中的变压器仿真
网络研讨会
Aug 25
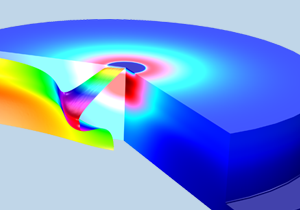
COMSOL® 中的半导体器件仿真
网络研讨会
Aug 22
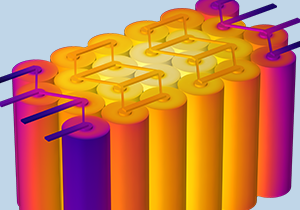
COMSOL® 中的锂电池仿真
网络研讨会
Aug 18
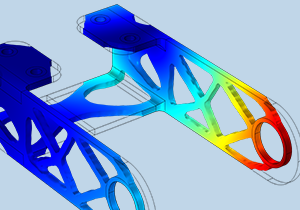
COMSOL® 的结构力学仿真
网络研讨会
Aug 15
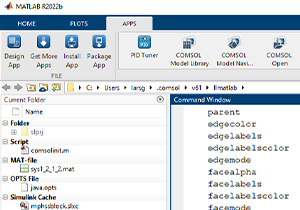
COMSOL® 中的 LiveLink™ for MATLAB® 和 LiveLink™ for Simulink® 功能简介
网络研讨会
Aug 11
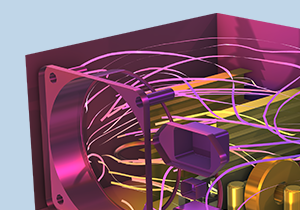
电子设备热管理的仿真分析
网络研讨会
Aug 04
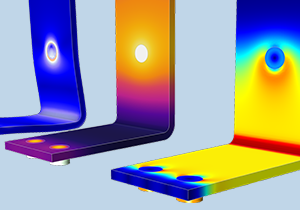
电磁损耗的仿真分析
网络研讨会
Jul 28
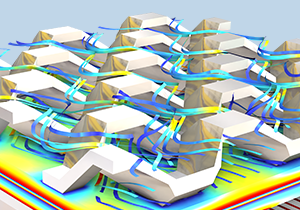
氢燃料电池与水电解槽的多物理场仿真
网络研讨会
Jul 25
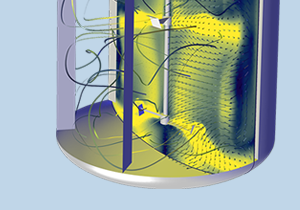
COMSOL® 中的多相流仿真
网络研讨会
Jul 21
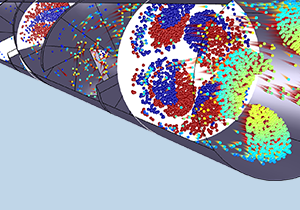
粒子追踪方法的建模仿真
网络研讨会
Jul 18
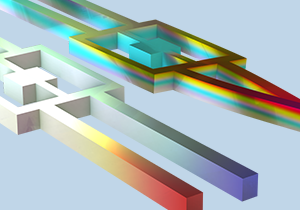
MEMS 器件的多物理场建模和仿真
网络研讨会
Jul 14
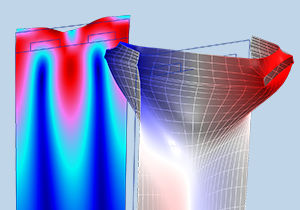
SAW 和 BAW 滤波器的建模仿真
网络研讨会
Jul 07
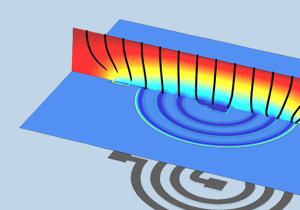
COMSOL® 中的电镀仿真
网络研讨会
Jul 04
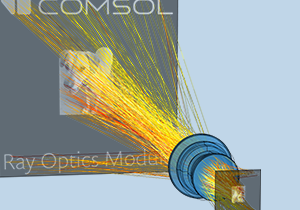
COMSOL® 中的射线光学仿真
网络研讨会
Jun 30
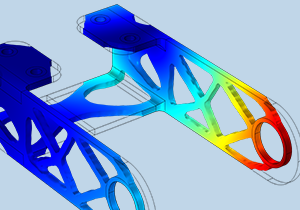
COMSOL® 中的热应力仿真
网络研讨会
Jun 16
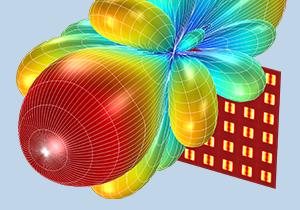
COMSOL® 中的高频电磁场仿真
网络研讨会
Jun 13
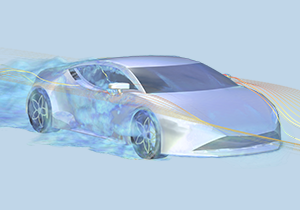
COMSOL® 中的流固耦合仿真
网络研讨会
Jun 09
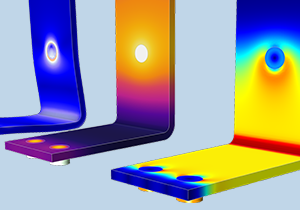
COMSOL® 中的传热仿真
网络研讨会
Jun 06
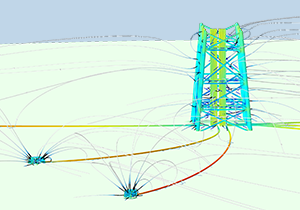
COMSOL® 中的腐蚀与防护仿真
网络研讨会
Jun 02
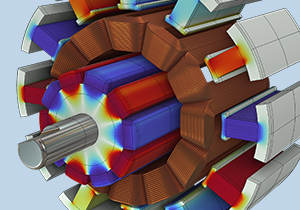
COMSOL® 中的低频电磁场仿真
网络研讨会
May 23
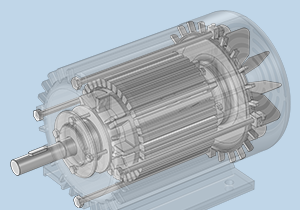
在 COMSOL® 中进行 CAD 导入及几何模型处理
网络研讨会
May 19
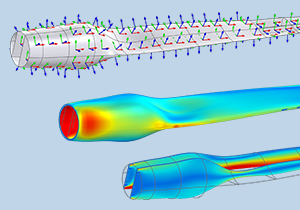
COMSOL® 中的复合材料仿真
网络研讨会
May 16
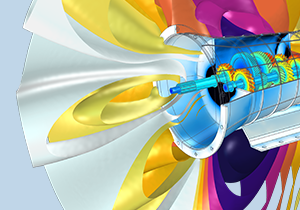
声学与振动的多物理场仿真
网络研讨会
May 12
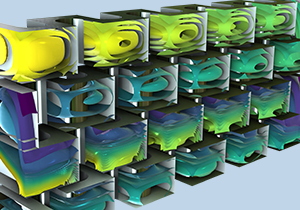
COMSOL® 化学反应工程仿真
网络研讨会
Apr 18
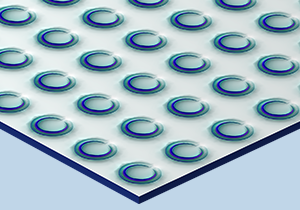
光学超材料仿真
网络研讨会
Apr 14
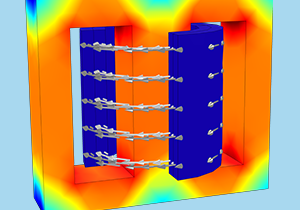
电力设备的多物理场仿真
网络研讨会
Apr 07
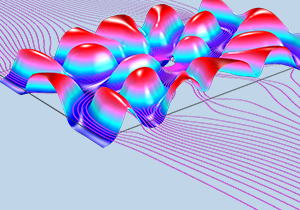
在 COMSOL® 中使用自定义函数建模
网络研讨会
Mar 31
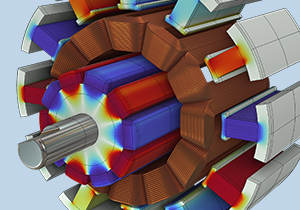
COMSOL® 6.1 电磁模拟新功能
网络研讨会
Mar 24
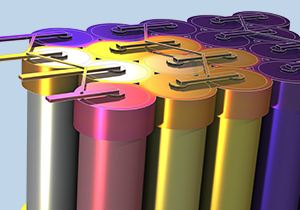
COMSOL® 6.1 电池模块新功能
网络研讨会
Mar 17
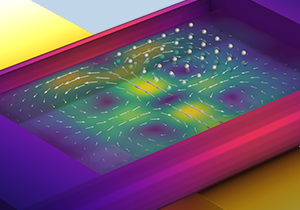
COMSOL® 中的声流仿真
网络研讨会
Mar 10
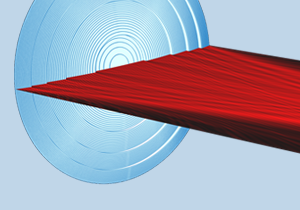
COMSOL Multiphysics® 波动光学仿真
网络研讨会
Mar 07
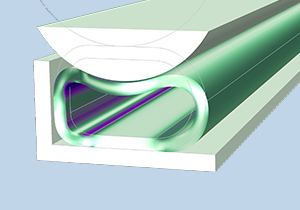
COMSOL® 6.1 结构力学模块新功能
网络研讨会
Mar 03
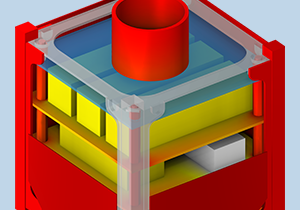
如何使用 COMSOL® 分析航天器热性能
网络研讨会
Feb 24
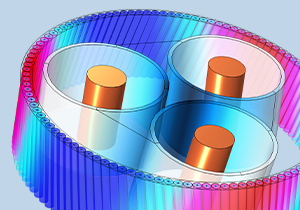
COMSOL® 6.1 模型管理器和 App 开发器新功能介绍
网络研讨会
Feb 17
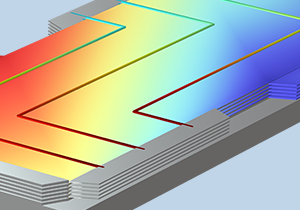
COMSOL® 6.1 燃料电池和电解槽模块新功能
网络研讨会
Feb 10
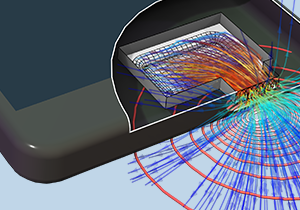
COMSOL® 6.1 声学模块新功能
网络研讨会
Feb 03
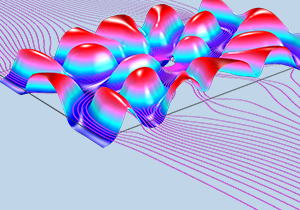
在 COMSOL® 中基于方程进行建模仿真
网络研讨会
Jan 13
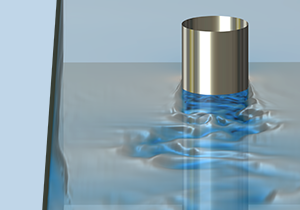
COMSOL® 6.1 CFD 模块新功能
网络研讨会
Jan 06
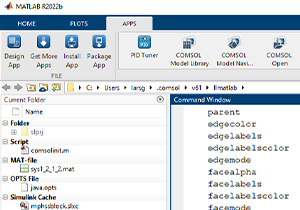
COMSOL LiveLink™ for MATLAB® 功能简介
网络研讨会
Dec 30

在 COMSOL® 中创建二维几何模型
网络研讨会
Dec 23
显示活动 6 场,活动总数 101 场。
Date | Title | Type | Host | Discipline |
---|---|---|---|---|
Dec 12 |
COMSOL® 中的传热仿真 |
网络研讨会 | COMSOL-线上 |
|
Dec 05 |
COMSOL® 中的多相流仿真 |
网络研讨会 | COMSOL-线上 |
|
Nov 28 |
COMSOL Multiphysics® 6.3 版本功能简介 |
网络研讨会 | COMSOL-线上 |
|
Nov 21 |
COMSOL® 中的转子动力学和多体动力学仿真 |
网络研讨会 | COMSOL-线上 |
|
Nov 14 |
COMSOL® 求解器介绍及设置方法 |
网络研讨会 | COMSOL-线上 |
|
Nov 07 |
使用 COMSOL Multiphysics® 模拟声学超材料 |
网络研讨会 | COMSOL-线上 |
|
Oct 24 |
多物理场仿真结果的处理与可视化 |
网络研讨会 | COMSOL-线上 |
|
Oct 17 |
COMSOL® 中的等离子体仿真 |
网络研讨会 | COMSOL-线上 |
|
Oct 10 |
COMSOL® 网格划分功能介绍 |
网络研讨会 | COMSOL-线上 |
|
Sep 19 |
电力变压器的多物理场仿真 |
网络研讨会 | COMSOL-线上 |
|
Sep 12 |
使用 COMSOL Multiphysics® 仿真高性能电机 |
网络研讨会 | COMSOL-线上 |
|
Sep 05 |
不确定性量化在多物理场仿真中的应用 |
网络研讨会 | COMSOL-线上 |
|
Aug 29 |
超声波及其应用的多物理场仿真 |
网络研讨会 | COMSOL-线上 |
|
Aug 15 |
使用 COMSOL Multiphysics® 模拟光电半导体 |
网络研讨会 | COMSOL-线上 |
|
Aug 08 |
COMSOL® 多物理场仿真加速数字岩心技术发展 |
网络研讨会 | COMSOL-线上 |
|
Aug 01 |
使用代理模型开发高效的 COMSOL® 仿真 App |
网络研讨会 | COMSOL-线上 |
|
Jul 25 |
COMSOL® 多物理场仿真在地热能开发中的应用 |
网络研讨会 | COMSOL-线上 |
|
Jul 18 |
COMSOL® 仿真 App 开发、部署和应用 |
网络研讨会 | COMSOL-线上 |
|
Jul 11 |
COMSOL® 中的光学仿真 |
网络研讨会 | COMSOL-线上 |
|
Jul 04 |
非线性结构材料参数估计 |
网络研讨会 | COMSOL-线上 |
|
Jun 27 |
基于 COMSOL® 构建电力设备的数字孪生 |
网络研讨会 | COMSOL-线上 |
|
Jun 20 |
COMSOL® 室内声学仿真 |
网络研讨会 | COMSOL-线上 |
|
Jun 13 |
COMSOL Multiphysics® 在半导体制造中的应用 |
网络研讨会 | COMSOL-线上 |
|
Jun 06 |
COMSOL Multiphysics® 在绿氢技术中的应用 |
网络研讨会 | COMSOL-线上 |
|
May 28 |
使用 COMSOL Multiphysics® 模拟放电现象 |
网络研讨会 | COMSOL-线上 |
|
May 16 |
使用 COMSOL® 模拟 SAW/BAW 器件 |
网络研讨会 | COMSOL-线上 |
|
May 09 |
COMSOL® 中的换热器仿真 |
网络研讨会 | COMSOL-线上 |
|
Apr 18 |
COMSOL Multiphysics® 中的流固耦合仿真 |
网络研讨会 | COMSOL-线上 |
|
Apr 11 |
多尺度电磁波仿真 |
网络研讨会 | COMSOL-线上 |
|
Apr 02 |
COMSOL® 微执行器和微型电机仿真 |
网络研讨会 | COMSOL-线上 |
|
Mar 26 |
COMSOL® 中的湍流仿真 |
网络研讨会 | COMSOL-线上 |
|
Mar 14 |
COMSOL® 仿真在电力电子技术中的应用 |
网络研讨会 | COMSOL-线上 |
|
Mar 12 |
COMSOL® 中的流体动压轴承仿真 |
网络研讨会 | COMSOL-线上 |
|
Mar 07 |
使用 COMSOL Multiphysics® 模拟 EMI/EMC 现象 |
网络研讨会 | COMSOL-线上 |
|
Mar 05 |
COMSOL® 中的热辐射仿真 |
网络研讨会 | COMSOL-线上 |
|
Feb 29 |
使用 COMSOL Multiphysics® 模拟 MEMS 加速度计和陀螺仪 |
网络研讨会 | COMSOL-线上 |
|
Jan 25 |
在 COMSOL Multiphysics® 中模拟腐蚀及防护系统 |
网络研讨会 | COMSOL-线上 |
|
Jan 18 |
使用 COMSOL® 模拟等离激元效应和超材料 |
网络研讨会 | COMSOL-线上 |
|
Jan 11 |
半导体封装和测试中的多物理场仿真 |
网络研讨会 | COMSOL-线上 |
|
Jan 04 |
COMSOL® 中的扬声器和麦克风仿真 |
网络研讨会 | COMSOL-线上 |
|
Dec 21 |
使用 COMSOL Multiphysics® 进行结构-热-光学耦合分析 |
网络研讨会 | COMSOL-线上 |
|
Dec 05 |
COMSOL® 多物理场仿真在电气绝缘中的应用 |
网络研讨会 | COMSOL-线上 |
|
Nov 30 |
微流体器件的多物理场仿真 |
网络研讨会 | COMSOL-线上 |
|
Nov 28 |
半导体制造中的晶体生长仿真 |
网络研讨会 | COMSOL-线上 |
|
Nov 21 |
COMSOL® 多物理场仿真在医疗设备研发中的应用 |
网络研讨会 | COMSOL-线上 |
|
Nov 16 |
COMSOL® 中的网格划分 |
网络研讨会 | COMSOL-线上 |
|
Nov 14 |
锂离子电池热失控仿真 |
网络研讨会 | COMSOL-线上 |
|
Nov 09 |
COMSOL® 中的磁流体仿真 |
网络研讨会 | COMSOL-线上 |
|
Nov 02 |
COMSOL® 地下水流及多孔介质流仿真 |
网络研讨会 | COMSOL-线上 |
|
Oct 31 |
电磁噪声的仿真分析 |
网络研讨会 | COMSOL-线上 |
|
Oct 27 |
使用 COMSOL Multiphysics® 仿真 PVD/CVD 薄膜沉积工艺 |
网络研讨会 | COMSOL-线上 |
|
Oct 20 |
COMSOL® 多物理场仿真优化电缆设计 |
网络研讨会 | COMSOL-线上 |
|
Oct 13 |
COMSOL® 的求解器简介 |
网络研讨会 | COMSOL-线上 |
|
Sep 26 |
COMSOL® 中的感应加热仿真 |
网络研讨会 | COMSOL-线上 |
|
Sep 19 |
COMSOL® 中的岩土力学仿真 |
网络研讨会 | COMSOL-线上 |
|
Sep 15 |
多物理场仿真在激光加工中的应用 |
网络研讨会 | COMSOL-线上 |
|
Sep 12 |
计算流体力学(CFD)多物理场仿真 |
网络研讨会 | COMSOL-线上 |
|
Sep 08 |
使用 COMSOL® 求解大型模型 |
网络研讨会 | COMSOL-线上 |
|
Sep 05 |
COMSOL® 中的声学超材料仿真 |
网络研讨会 | COMSOL-线上 |
|
Sep 01 |
使用 COMSOL Multiphysics® 进行设计优化 |
网络研讨会 | COMSOL-线上 |
|
Aug 29 |
COMSOL® 的压电材料和器件仿真 |
网络研讨会 | COMSOL-线上 |
|
Aug 25 |
COMSOL® 中的变压器仿真 |
网络研讨会 | COMSOL-线上 |
|
Aug 22 |
COMSOL® 中的半导体器件仿真 |
网络研讨会 | COMSOL-线上 |
|
Aug 18 |
COMSOL® 中的锂电池仿真 |
网络研讨会 | COMSOL-线上 |
|
Aug 15 |
COMSOL® 的结构力学仿真 |
网络研讨会 | COMSOL-线上 |
|
Aug 11 |
COMSOL® 中的 LiveLink™ for MATLAB® 和 LiveLink™ for Simulink® 功能简介 |
网络研讨会 | COMSOL-线上 |
|
Aug 04 |
电子设备热管理的仿真分析 |
网络研讨会 | COMSOL-线上 |
|
Jul 28 |
电磁损耗的仿真分析 |
网络研讨会 | COMSOL-线上 |
|
Jul 25 |
氢燃料电池与水电解槽的多物理场仿真 |
网络研讨会 | COMSOL-线上 |
|
Jul 21 |
COMSOL® 中的多相流仿真 |
网络研讨会 | COMSOL-线上 |
|
Jul 18 |
粒子追踪方法的建模仿真 |
网络研讨会 | COMSOL-线上 |
|
Jul 14 |
MEMS 器件的多物理场建模和仿真 |
网络研讨会 | COMSOL-线上 |
|
Jul 07 |
SAW 和 BAW 滤波器的建模仿真 |
网络研讨会 | COMSOL-线上 |
|
Jul 04 |
COMSOL® 中的电镀仿真 |
网络研讨会 | COMSOL-线上 |
|
Jun 30 |
COMSOL® 中的射线光学仿真 |
网络研讨会 | COMSOL-线上 |
|
Jun 16 |
COMSOL® 中的热应力仿真 |
网络研讨会 | COMSOL-线上 |
|
Jun 13 |
COMSOL® 中的高频电磁场仿真 |
网络研讨会 | COMSOL-线上 |
|
Jun 09 |
COMSOL® 中的流固耦合仿真 |
网络研讨会 | COMSOL-线上 |
|
Jun 06 |
COMSOL® 中的传热仿真 |
网络研讨会 | COMSOL-线上 |
|
Jun 02 |
COMSOL® 中的腐蚀与防护仿真 |
网络研讨会 | COMSOL-线上 |
|
May 23 |
COMSOL® 中的低频电磁场仿真 |
网络研讨会 | COMSOL-线上 |
|
May 19 |
在 COMSOL® 中进行 CAD 导入及几何模型处理 |
网络研讨会 | COMSOL-线上 |
|
May 16 |
COMSOL® 中的复合材料仿真 |
网络研讨会 | COMSOL-线上 |
|
May 12 |
声学与振动的多物理场仿真 |
网络研讨会 | COMSOL-线上 |
|
Apr 18 |
COMSOL® 化学反应工程仿真 |
网络研讨会 | COMSOL-线上 |
|
Apr 14 |
光学超材料仿真 |
网络研讨会 | COMSOL-线上 |
|
Apr 07 |
电力设备的多物理场仿真 |
网络研讨会 | COMSOL-线上 |
|
Mar 31 |
在 COMSOL® 中使用自定义函数建模 |
网络研讨会 | COMSOL-线上 |
|
Mar 24 |
COMSOL® 6.1 电磁模拟新功能 |
网络研讨会 | COMSOL-线上 |
|
Mar 17 |
COMSOL® 6.1 电池模块新功能 |
网络研讨会 | COMSOL-线上 |
|
Mar 10 |
COMSOL® 中的声流仿真 |
网络研讨会 | COMSOL-线上 |
|
Mar 07 |
COMSOL Multiphysics® 波动光学仿真 |
网络研讨会 | COMSOL-线上 |
|
Mar 03 |
COMSOL® 6.1 结构力学模块新功能 |
网络研讨会 | COMSOL-线上 |
|
Feb 24 |
如何使用 COMSOL® 分析航天器热性能 |
网络研讨会 | COMSOL-线上 |
|
Feb 17 |
COMSOL® 6.1 模型管理器和 App 开发器新功能介绍 |
网络研讨会 | COMSOL-线上 |
|
Feb 10 |
COMSOL® 6.1 燃料电池和电解槽模块新功能 |
网络研讨会 | COMSOL-线上 |
|
Feb 03 |
COMSOL® 6.1 声学模块新功能 |
网络研讨会 | COMSOL-线上 |
|
Jan 13 |
在 COMSOL® 中基于方程进行建模仿真 |
网络研讨会 | COMSOL-线上 |
|
Jan 06 |
COMSOL® 6.1 CFD 模块新功能 |
网络研讨会 | COMSOL-线上 |
|
Dec 30 |
COMSOL LiveLink™ for MATLAB® 功能简介 |
网络研讨会 | COMSOL-线上 |
|
Dec 23 |
在 COMSOL® 中创建二维几何模型 |
网络研讨会 | COMSOL-线上 |
|
显示活动 101 场,活动总数 101 场。
- 应用案例
- 案例下载
- 产品演示视频
- 用户案例
- 论文和技术资料
- COMSOL 相关书籍
- |
- 隐私政策
- |
- 商标
- |
- Cookie Settings
- 沪ICP备14030237号-1
- © 2024 by COMSOL. 版权所有