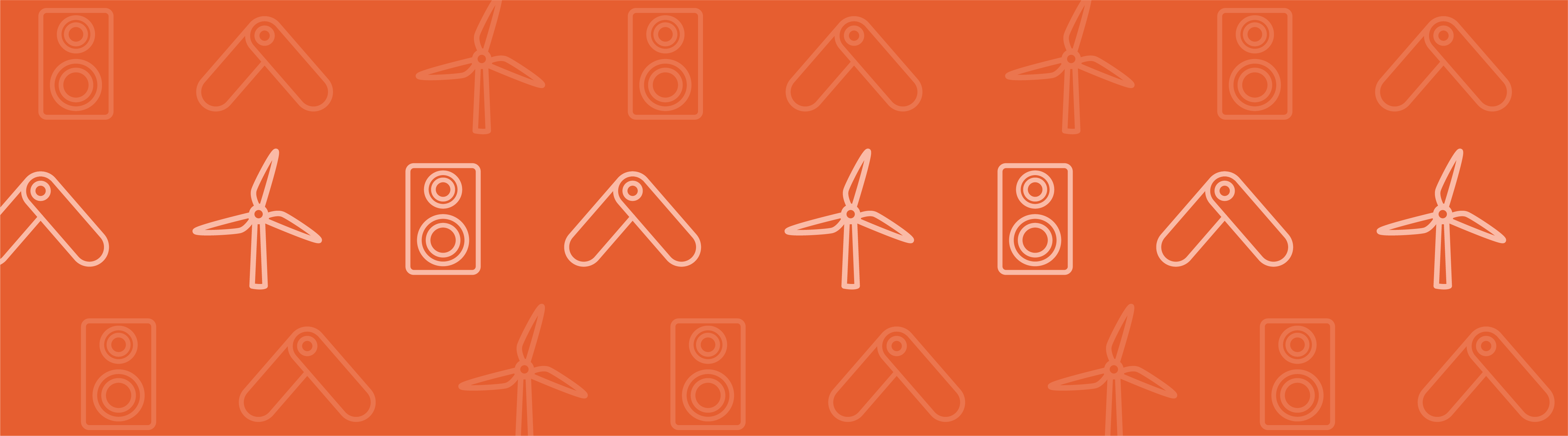
一直以来,在 COMSOL 博客及科技界中 3D 打印(增材制造)都是一个热门话题。科技创新进一步推动了该项技术的发展,拓展了它在不同领域中的研究、制造及设计应用。借助 COMSOL Multiphysics 的强大功能,荷兰应用科学研究部(TNO)的科技人员正在研究 3D 打印在材料设计领域的应用前景。
更加灵活和自由的 3D 打印
自问世以来,3D 打印技术的影响已经渗透到了各行各业,比如汽车制造商。3D 打印使汽车设计变得更自由,它支持对零件进行高度定制,同时还能节省生产时间及成本。这项技术还促进了医药行业的创新,支持对植入物及器件进行定制设计,并能制作出器官的精确复本。
3D 打印机正在打印一个产品零件。
正如我们看到的,增材制造已经成为一项高效的产品开发手段。随着技术的进步,更加自由和灵活的设计不断涌现,进一步拓宽了该技术的应用范围;材料设计正是其中一个极具潜力的应用领域。
材料设计特别适用于裁剪具有重复样式的精细结构,为产品设计出最优的性能。根据要求,从简单的单片几何到复杂的多材料几何,均可采用单个微结构(或称晶胞)的设计。从理论上讲,晶胞设计的复杂度也就是设计的自由度,仅仅受限于设计人员的创造性和制造能力。
一直以来,3D 打印仅支持打印单材料产品,不过,该技术的最新发展使得小型结构的多材料打印成为可能。该技术使设计人员能够更精细地控制微结构,并能根据具体要求对微结构进行组合和定制。此外,工程师还能选择结构中所用某种材料的比例和排列。
TNO 的研究人员正结合多尺度模拟与多物理场仿真来分析 3D 打印中的虚拟材料设计。下一节,我们将更详细地分析他们的创新设计。
利用 COMSOL Multiphysics 分析虚拟材料设计
开始仿真研究前,团队首先设计了单个晶胞,该晶胞在一个方向上的刚度是另一个方向的两倍,然后分析了给定几何下的材料行为。借助 COMSOL Multiphysics 的优化功能,团队能够分析出与给定应变相匹配的应力大小,从而用于他们想要的刚度矩阵。他们在一个用于测试材料行为的打印样品上验证了结果。
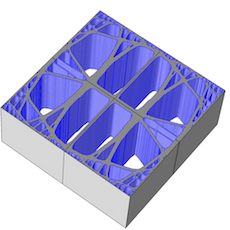
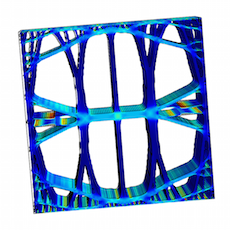
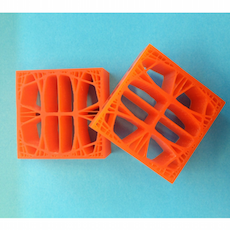
左:晶胞几何。中:优化设计中的机械应力。右:3D 打印样品。
研究人员随即在具有高度各向异性的材料中进行了一个类似的研究。通过仿真,他们能够控制材料的空间分布和各向异性纤维的取向。
团队还有一个更宏大的目标,希望将仿真拓展到由不同材料组成的微结构中。他们对结构中各种材料的组分及分布进行了调整,直到实现了最优的导热系数。
用于实现理想各向异性导热系数的多材料成分。白色表示高导热区域、橙色代表低导热区域,红色为非导热材料和孔隙。
在微观级别实现优化后,TNO 团队又开始研究更大尺度对象的优化。虽然这在实际产品开发中是必须的一步,但将微结构的仿真结果拓展到实际产品尺寸的计算成本会很高。多尺度模拟提供了一种解决方案,它支持设计人员同时在微材料和产品尺度展开模拟。团队提取了能在多个多材料单元中实现等效结构行为的几个参数,然后将其用作器件全尺度模型的输入项。
从产品设计优化到完整零件
虽然拓扑优化是生成 3D 打印设计的一项强大工具,但当涉及具体增材制造技术时,它仍存在一些局限。例如,在选择性激光熔化成形(SLM)技术中,打印机会利用激光将材料粉末熔化为所需的形状。之后,必须移除打印对象上未使用的粉末,此外,SLM 设计中通常会避免使用大的悬臂,因为它会发生弯曲。
为解决这一问题,研究团队设计了具有不同密度的晶胞,然后对其结合以便实现产品层级所需的整体属性。他们在 COMSOL Multiphysics 中结合了多项技术,包括从单个晶胞类型的刚度均化到产品层级的拓扑优化。随后,他们在聚合物锤柄的开发中应用了整套工艺,如下图所示。设计中包含微观级别的不同晶胞类型,同时优化得到适合的刚度和最少的材料用量。
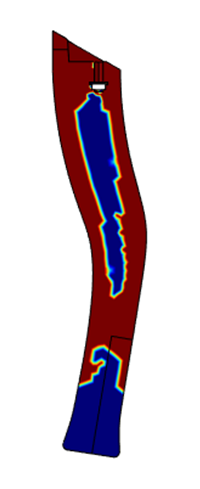
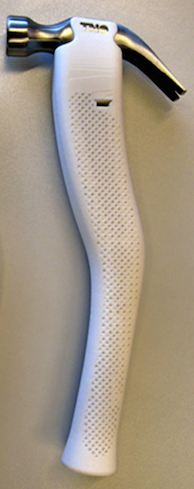
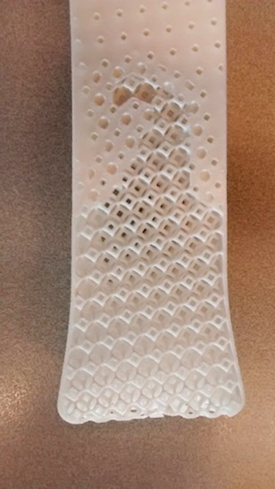
左:拓扑优化的仿真结果。中:优化的锤柄设计。右:包含多个晶胞类型的样式。靠近顶部处的晶胞分布最密,对应较小孔隙,底部的晶胞分布最为稀疏。中间有一些过渡形状。
增材制造中的新可能
TNO 的研究人员已证明当前增材制造中的各种局限可以通过多尺度模拟与多物理场仿真有效解决。这些进步有助于将 3D 打印的优势与覆盖范围延伸到常规技术之外;从而能开发出更复杂的新产品,使更多行业可以从 3D 打印中受益。
扩展阅读
- 如希望了解 TNO 仿真研究的详细内容,您可以阅读《COMSOL News》 2015第 22 页的文章
- 浏览 3D 打印专题的其他相关博客
评论 (0)